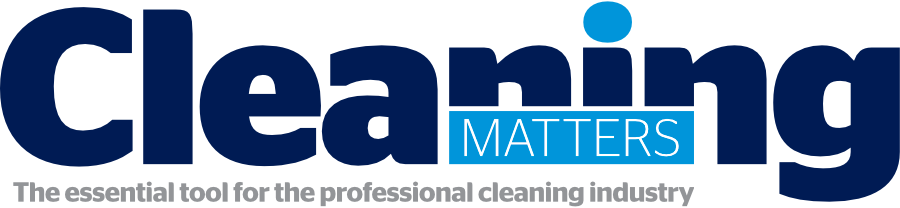
![]() |
Chris Shaw
Editor |
Home> | WASHROOM HYGIENE | >Dispensers | >Cutting down costs in FM |
Home> | CATERING & FOOD HYGIENE | >Equipment & Services | >Cutting down costs in FM |
Cutting down costs in FM
22 May 2015
Charlotte Branwhite from Tork manufacturer SCA looks at smart ways of reducing both labour and product costs in the cash-conscious FM sector.
Everyone who works in the FM sector is aware that cost is king. The pressure is always on to choose low-cost products since building-owners need to keep their eye on the bottom line. But sometimes the cheapest product can be surprisingly expensive in use. This is particularly true of consumables such as washroom products and disposable catering wipers.
Both are essential in facilities such as hospitals, schools, large offices and institutions. But it is important to look at the ways these products are used and the labour costs involved as well as the purchase price.
Hidden costs
Take toilet tissue for instance. This comes in a variety of formats with one of the cheapest being low-cost conventional rolls from the cash and carry. But however cheap these may be, their cost in use will be disproportionately high in a sizeable institution.
First there will be the labour costs involved unpacking them and fitting them into individual dispensers, then changing them whenever a roll has been used up. Some facilities get around this by storing loose rolls on the cistern. But such rolls frequently end up on the toilet floor where they will become soiled, wet and unusable which means a great deal of waste will occur.
When a cheap and flimsy roll is supplied, too, the amount of paper taken by each visitor is likely to be excessive. And in a vulnerable setting such as a school or institution, loose toilet rolls may be pilfered, thrown around or put down the toilet where they will cause blockages.
Similarly C-fold towels – either supplied in a dispenser or left on the washroom unit – are a low-cost hand drying option that can prove surprisingly expensive in use. C-fold towel dispensers make it difficult for visitors to take out one towel at a time and instead the towels tend to be removed in clumps, which quickly drives up costs. When towels are left exposed on the unit, the visitor may take just one or two – then drip their wet hands on to the rest making them soggy and unusable.
Besides the problems of over-consumption and waste, these situations will also lead to a mess on the units and the floor and perhaps blocked toilets as well, leading to added cleaning and plumbing costs.
In the catering kitchen, too, loose wiping rolls may be supplied to enable staff to wipe surfaces, clean their hands, mop up spills etc. But if the roll is left out on the kitchen surface it may become contaminated with liquids, meat juices or allergens which will render it unusable.
Control consumption
FM managers can greatly reduce costs by equipping their premises with dispensers for hand towels, toilet tissue and catering rolls because a good dispensing system will prevent the user from taking out more product than they need. It will also protect the product from contamination before use and reduce the issue of waste.
Consumption control has a snowball effect. Where lower amounts of product is used, less labour time is spent replacing it. And where the paper is protected from contamination, less time will be spent on cleaning away spoiled products which means that waste disposal costs will be lower.
A good example is the Tork Matic Hand Towel Roll Dispenser. This protects the hand towels before use and gives out only one towel at a time. This reduces waste, product and labour costs since the dispenser is easy to refill and also holds sufficient paper for up to 1,400 hand dries. The Tork SmartOne toilet tissue system also offers single-sheet dispensing and deters washroom users from taking out excess paper. Tests have shown that the Tork SmartOne can help facilities reduce consumption by up to 40%.
So FM managers should beware the risk of simply looking at the price tag when buying their consumables. Factors such as cost in use, waste, maintenance levels, consumption, re-ordering frequency and labour costs all need to be weighed up when making a final purchasing decision.