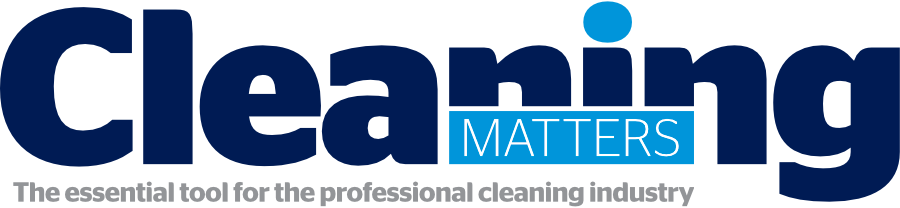
![]() |
Chris Shaw
Editor |
Home> | SUSTAINABILITY | >Green Cleaning Methods | >Cleaning sustainability during COVID-19 |
Home> | SUSTAINABILITY | >Green Cleaning Products | >Cleaning sustainability during COVID-19 |
Home> | WASHROOM HYGIENE | >Hand Hygiene | >Cleaning sustainability during COVID-19 |
Cleaning sustainability during COVID-19
15 February 2022
Businesses large and small rushed to introduce additional and stricter cleaning and hygiene processes during the COVID-19 pandemic. This had an impact on the focus on sustainability as Lynne Snoding explains.

THE OVERRIDING requirement has been to protect customers and staff while also providing additional reassurance by cleaning more frequently and more visibly. Ready-to-use products have offered an excellent solution to the immediate challenge. But those same businesses want to operate sustainably and control their costs. No matter how long the current emergency lasts professional ultra-concentrate formulations can help them meet these requirements.
Ready-to-use products can be ideal for temporary use and occasional tasks: they are convenient, easy to introduce, and readily available. This in part explains why businesses have used them during the pandemic. But costs can mount up in the long run and especially when they are used frequently.
Ultra-concentrated products
Businesses with established cleaning procedures often turn instead to ultra-concentrated products in conjunction with dosing or dilution equipment. Cleaning solutions are prepared accurately and consistently on-site by adding water to a reusable spray bottle, wash bucket or sink. The cost of each is much less than using ready-to-use products. For example, a spray bottle of surface cleaner prepared this way might cost tens of pence while the same size ready-to-use equivalent could easily be two or three pounds.
Cleaning teams can quickly, easily, and economically prepare solutions for equipment such as spray and toilet bottles, sinks, buckets, or cleaning machines. The result is safe, simple, and consistent high-performance cleaning while minimising wastage, packaging, and chemical miles.
One of the main reasons ultra concentrates deliver reduced cost in use is that solutions are prepared at the optimum dilution for superior and consistent performance. This reduces the need for repeat cleaning which cuts wasted time, delivering an immediate productivity and efficiency gain. Considering the product contributes far less to the overall cost than the person doing the cleaning it makes sense to use products that maximise performance and productivity.
Ultra concentrates also reduce the amount of product wastage because, unlike old-fashioned “pour-and-glug”, there is no guesswork involved in preparing solutions. Costs are reduced and predictable.
Another saving is made with packaging because water is added at the point of use, rather than the place of manufacture. One pack of ultra-concentrate can contain enough product to make the same amount of solution as dozens or hundreds of comparable bulk or ready-to-use products.
A business using 100 cases of six 750ml single-use spray bottles could reduce plastic waste by up to 125.6kg (99.6% reduction) and up to 26.6kg less cardboard (98.9% reduction) by switching to Diversey’s ultra concentrates and re-usable bottles. Changes like these also reduce supply chain burdens because fewer cases need to be bought, transported and stored to support any given operation. Transportation costs can be up to 20 times less and warehouse and on-site storage requirements up to 22 times lower. Waste management and recycling costs are also reduced because there is less packaging to handle.
Investment and opportunities
Investment is required with any dosing or dilution system. This can include the cost of the equipment and training staff. However, this investment is repaid by the savings made with lower cost-in-use, reduced wastage, and improvements in consistency that save time and money. Reputable suppliers will offer detailed projections to show how and when their products return on the investment. It is often much quicker than businesses expect.
Any change of product also presents the opportunity to use a new and – hopefully - better formulation with sustainability benefits. The most obvious benefit can come from simply adopting formulations containing more sustainable ingredients. There are numerous sustainability accreditations including the EU Ecolabel, Nordic Swan, and AISE Chartermark that are applied to cleaning products. Products with these accreditations have undergone rigorous evaluation to ensure they meet a variety of sustainability criteria.
Another way to make a quick sustainability gain is to switch to formulations that work at lower temperatures. These save on gas or electricity costs associated with heating water. Switching to a lower temperature laundry product, for example, can save around 35% on water heating costs, consume 34% less water and cut wash time by almost 20% - all excellent sustainability gains. Any savings made will go straight to the bottom line.
Further sustainability benefits arise from replacing two or more products with multipurpose formulations. This saves on procurement costs and reduces supply chain complexity because fewer different items are sourced, transported, and stored. Cleaning processes are generally simpler because one product is used instead of two or more. That often leads to higher compliance levels, improved standards, and better results. Training burdens are also reduced because staff need to learn about fewer different products. Gains in these areas can be more difficult to quantify but the long-term benefits are nevertheless real and, with support from suppliers, they can be predicted and measured.
Ready-to-use products have offered an excellent solution to the immediate challenge of providing additional infection prevention measures during the pandemic. In the longer term, solutions based on professional ultra-concentrate formulations and accurate dosing and dilution equipment can offer a number of sustainability benefits.
Hand hygiene challenges
Frequent hand cleaning or disinfection is one of the most effective ways to stop the spread of the virus that causes COVID-19. Businesses have adopted more stringent hand hygiene processes during the pandemic, and many have placed extra hand hygiene stations in their washrooms and elsewhere. These typically utilise pump-action bottles to dispense alcohol-based disinfectant hand rub. This is quick and practical, but could longer term solutions be more effective and economic?
Studies show that people dispense more product than needed if they are free to decide for themselves. Many of us take multiple shots from a dispenser “just to be sure” when one is usually enough. Bottles are emptied quicker than necessary which can be expensive because they must be replaced or refilled more often. Perhaps more importantly, it increases the risk that other people will be unable to disinfect their hands when they should. And there is always the risk that portable bottles will go missing.
Professional wall or floor mounted dispensers and products offer many long-term cost and operational benefits. Generally, they deliver better dosing accuracy and consistency. In the long run that means lower costs and better predictability. This alone can often justify the investment.
Well-designed dispensers also help maximise and maintain product availability so that as many people as possible can disinfect their hands. Because they are generally fixed in position, they will always be in the correct location for convenient and appropriate use and less likely to go astray. Features such as alerts or easy product level checks help ensure dispensers are refilled before they are empty. Using larger containers should, all else being equal, extend the time between refills which also reduces the risk of non-availability.
Dispensers and contactless operation
The latest-generation dispensers offer contactless operation. That is good for hand hygiene because it reduces the risk of cross-contamination between users. Uniquely, the dispenser switches automatically to manual operation if its batteries become discharged. This risk is reduced because the equipment can alert staff members when its battery or product levels get too low.
Diversey offers a complete range of soaps, sanitisers, and foams for use with IntelliCare. These include formulations that meet the all-important EN14476 virucidal standard against enveloped viruses, including SARS-CoV-2 that causes COVID-19. IntelliCare supports complete product interchangeability because all products are available in the same size high-capacity containers. For example, dispensers in washrooms can be used with soaps while identical units in public areas are used with disinfecting hand rubs. Businesses can install, relocate, or reconfigure their dispensers at any time.
Another benefit of the system is dual-dosing capability. This allows, for example, dispensers in restricted areas to be set at a lower dose for staff who have been trained to apply hand rubs or soaps correctly. Dispensers in public areas can be set to deliver a larger single dose for casual users who might be less aware of correct processes. This helps to control costs while maintaining the highest hygiene standards.
Hand hygiene is often the first line of defence against many infections. It is even more critical when one of these – like SARS-Cov-2 - is so deadly and spread so easily. Leading suppliers such as Diversey can help customers choose the right dispensers and products to make hand hygiene and disinfection as simple and convenient as possible.
Lynne Snoding is sector marketing manager, BSC, Diversey, UK & Ireland
For more information visit www.diversey.com
- New cleaning weapon in the fight against graffiti
- Is your restaurant at risk?
- Failing to prepare is preparing to fail
- Mobile auditing upgrade
- Reduction in chemicals at campus
- Lining up on the Water Technology List
- Clever cleaning
- Safer floors in winter, better floors all year round
- Hands-down winner
- Boosts membrane cleaning flexibility
- Chemical free attraction
- More water efficient scrubber dryers on ECA scheme
- Council cleaners go bleach free to green up Liverpool
- Green at source
- Scheme saves water, saves money, saves tax
- Ioning out chemicals in cleaning
- Wipe out waste with contaminated wipes laundry service
- Companies partner for green paper drive
- Good reaction to environmental best practice awar
- A cool half