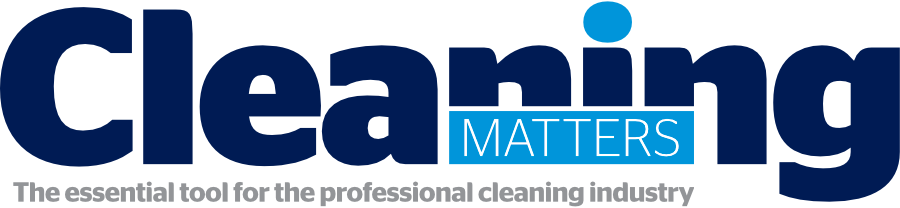
![]() |
Chris Shaw
Editor |
Home> | CONTRACT CLEANING | >Contractors | >Put people first for better cleaning outcomes |
Home> | CONTRACT CLEANING | >Suppliers | >Put people first for better cleaning outcomes |
Put people first for better cleaning outcomes
03 January 2025
A tailored, people-focused design approach to cleaning machine solutions is needed to help the sector overcome workforce challenges, drive up productivity and support sustainability ambitions. Ian Buckle explains why.

BUSY CLEANING operations face a specific challenge - one that impacts many areas including operational efficiencies, cost control, and resource planning. That challenge is focused on people.
Cleaning operatives often work long shifts, in physically and mentally draining working environments. They also do so using heavy and often cumbersome cleaning equipment.
According to the Health and Safety Executive, nearly half a million UK workers suffer from work-related musculoskeletal disorders that typically impact the back, shoulders and neck, with manually manipulating heavy wheeled loads one of the primary factors for overexertion and fatigue.
This is particularly pertinent in the cleaning sector. And, as a result, the sector constantly battles with workforce churn and high levels of staff absenteeism.
This isn’t a new problem. The cleaning sector’s people problem is long-standing and has been compromising its workforce strength due to unplanned absences and staff shortages for some time. It can mean shift patterns need to be continually altered, delays to cleans, failure to deliver contracts or meet SLAs, and in some cases, financial penalties.
However, with 80% of a cleaning company’s costs linked to its labour function, tackling the underlying causes of labour disruption and exposure to workforce weakness is key.
So, how does the sector find the workforce solutions it needs to tackle staff absenteeism, build workforce resilience, and maximise operational efficiency?
Using insight to drive machine innovation
For a long time, the industry has typically focused on developing machine technology that improves cleaning performance. However, that focus places the machine itself at the centre of design thinking, rather than the individual operating the machine.
A new approach is needed – one that places the user at the heart of cleaning machine product design. This is something we’re starting to see in emerging, innovative solutions – which have been developed based on in-depth sector research, extensive field tests, and consumer feedback.
Through our own research, we uncovered the top five challenges the cleaning sector is facing, which guide this focus on people-led design thinking:
- Completing jobs on time
- Maximising productivity
- Tackling workforce fatigue and potential muscular injuries
- Minimising downtime and extending machine lifecycles
- Improving sustainability, by reducing waste and optimising cleaning outcomes.
Addressing these challenges requires an intuitive, adaptable, easy-to-use, and ergonomically designed cleaning machine.
Putting people at the heart of design
The cleaning industry encompasses a range of people – with unique needs, skill levels and work experience. Today’s cleaning machine solutions – which are often operated by multiple users – need to address these differences, adapting simply and effectively to individual user needs.
There are so many ways this can be done, but one of the key issues to address – if we are to influence staff absenteeism – is ergonomic flexibility. Modern cleaning machine solutions need to be adaptable to the different height and weight of users, for example. This offsets the physical stresses placed on staff while operating the machinery, reducing the risk of fatigue and muscle-related problems or injuries, a leading cause of staff absenteeism.
Additionally, the introduction of a personalised digital interface, which can be programmed specifically for individual users, accessed via a pin code, means cleaning operatives can quickly prepare for their shift and have confidence that their skill levels have been accounted for.
To improve sustainability and optimise resource-use, cleaning machines can automate the application of chemical and water use. This not only takes responsibility away from cleaning operatives, who may be inexperienced in judging optimal resource consumption, but it also ensures the perfect balance of materials are used – reducing waste, saving costs, and improving sustainability performance.
Finally, built-in intuitive controls that are pre-calibrated, alongside quick start functionality, enable tasks to be started on time to drive up productivity.
A cleaning machine designed with people at its heart will reduce injury and staff absenteeism. This harmonises the physical and digital world on a new breed of cleaning machines, which are truly supportive to the operatives the cleaning sector relies upon.
Ian Buckle, is head of brand and design at Nilfisk
For more information, visit: www.nilfisk.com