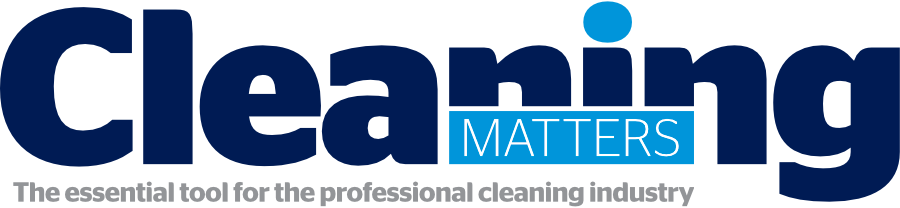
![]() |
Chris Shaw
Editor |
Home> | GENERAL EQUIPMENT & SERVICES | >IT & Software | >Work smarter not harder |
Home> | GENERAL EQUIPMENT & SERVICES | >Technology & Innovation?Services | >Work smarter not harder |
Work smarter not harder
08 July 2014
Is Google Glass going to become standard for cleaning operatives? Will all cleaning machines contain tracking devices for remote monitoring? Catherine Christie examines the new 'intelligent technologies'
If the innovations launched at ISSA/INTERCLEAN Amsterdam are anything to go by, the cleaning industry is undergoing a technological transformation towards more intelligent cleaning.
As contract cleaners and facility management companies come under constant pressure to increase operational efficiency, integrate new services and become even more professional to stay competitive and profitable, manufacturers are realising that it is no longer enough to simply offer them products. Solutions are required that bring added value through better managerial control and oversight of how that product is used. Not only can this lead to a reduction in cleaning costs, it can also improve health and safety, enhance staff training and increase sustainability.
Dr Ilham Kadri, president of Sealed Air Diversey, explains: "The biggest cost in the cleaning industry is labour, which accounts for approximately 80% of costs. If we can make staff more productive and work safer by providing easy-to-use innovations that also don't waste water and electricity in the process, it's a big win for this industry and across the value chain. We also want solutions to give employers peace of mind that they are managing risk in their client's operation."
Web-based technologies can track, monitor and manage the way a product is used. From the development of mobile devices and apps to the installation of small sensors in equipment and tracking devices in machines, these solutions turn data into insight to provide businesses with the knowledge to make better decisions.
Washroom monitoring
A key area of development for web-based technology is in the washroom. Launched at ISSA/INTERCLEAN Amsterdam, Tork EasyCube from SCA Hygiene Products provides facility managers with live insights into the day-to-day needs of a facility. By placing a small sensor into equipment such as a soap-or toilet roll dispenser, the system can track and analyse washroom usage, refill requirements and traffic trends to provide an instant overview of the state of the washrooms to an office computer or in the field via smartphones and tablets. The system also features a 'load the trolley' function that helps to ensure the operative has the right equipment on their cleaning rounds.
"One of the first companies to trial this only had one report in six months of an empty dispenser," Åsa Kalentun, director of European product management at SCA Hygiene Products, says.
As well as helping FM companies to enhance their service, Kalentun adds that the system can decrease costs by moving cleaners away from static cleaning schedules. "Cleaners save time and energy as they only need to visit the washrooms that the system shows need attention rather than check every single one."
Kalentun concludes: "In the future, the mobile phone will be an obvious tool for a cleaner. The FM company responsible for a big building will want to know what's happening and share this with the customer so that they know cleaning has taken place and is of a high quality. It's about working smarter not harder and it empowers the cleaning operatives to focus on the things that matter. This is only the start and we will continue to develop this."
As well as providing useful insights about visitors and usage for cleaning providers, Bloe – SCA's new toilet and urinal service solution – also demonstrates how web-based technology can be used to provide an elevated washroom experience for end-users. Based on real-time data from connected toilets and urinals, it includes integrated screens for visual communications towards visitors, and features to automatically facilitate cleaning, control odours and reduce water usage. For example, a ventilation system with aromatic oils creates an invigorating fragrance throughout the washroom. Roll out of these SCA products in other European markets will start in 2015.
Occupational skincare provider Deb Group has also introduced a new Dispenser Monitoring System designed to benefit both facilities management providers and their customers. The network of wireless-enabled dispensers, compatible with Deb’s full range of foaming soaps, transmits usage data to a server, predicting product usage and replacement to facilitate workflow planning and efficiency.
XIBU sense MANAGEMENT from Hagleitner Hygiene International also helps facility managers to check the filling level of dispensers and the cleaning activities of staff members in real-time, no matter where they are. "This software solution leads to frequency-oriented service, lean-cleaning organisation and control as well as to cost-effective staff deployment," the company says.
Fleet management
Fleet management systems had a strong presence at ISSA/INTERCLEAN. By fitting scrubber-driers and sweepers with a telematics box that connects the machine's information to the Internet, companies can use GPS and mobile telephony to find out where their machines are deployed, when they have been used to perform what work, and what condition they are in. This lays the foundation for optimisation and increased efficiency of everyday work routines.
Tennant, which launched IRIS (Intelligent Remote Information System) Technology in the US last year, is now rolling it out globally in approximately 70% of its walk-behind scrubber portfolio and looking to expand its capabilities. This machine-to-machine telemetry communications device pulls hours off the machine to schedule service, sends email communication to customers notifying them to replace parts, and provides visibility to machine utilisation, such as the number of hours used per day to compare usage across multiple machines. This machine data is critical to making well-informed service decisions, according to the company.
Rusty Zay, Tennant's senior vice president global marketing, says: "Contractors are under pressure to produce the same service or better for less money and they have to be more sustainable. So, they need big changes to make these razor-thin margins and to find ways where they can differentiate themselves over the long-term. In-house cleaners are also under pressure to stay within tight budgets. The better insights that you can have into your business, the more value you can provide for your customer and the more value for your organisation, and that's what IRIS technology provides."
The new ICE (Intelligent Cleaning Equipment) SMART line range of scrubber-driers from Worldwide Cleaning Support contains new technology I-Synergy, which collects operational data from cleaning machines and transmits the information to an International Cleaning Equipment server. From the server, daily reports can be generated and sent to the end user via email. These emails contain a range of information about the usage of the machine, from operational times to faults.
John Elmore, managing director of Worldwide Cleaning Support, says that this ability to monitor and manage equipment remotely is playing an important part in helping to lower the cost of cleaning machine ownership. He adds: "A team leader can monitor the usage of the machine to ensure optimal productivity or a hire company can be alerted to any faults or breakdowns a machine may have so that they can either exchange or repair a machine as soon as possible and keep their customer satisfied.
"This information also helps assist the engineer that will be repairing the machine, as they already know the details of the fault and can therefore repair the machine upon the first visit. A further advantage is complete machine control. Every machine that is owned can be controlled from the central server, which allows machine owners to shut down the machine in case of emergency or theft."
Other businesses to recently develop solutions for managing fleets of cleaning machines include Kärcher (Kärcher Fleet), HAKO (Hako-Fleet-Management-Solutions) and Diversey Care (TASKI IntelliTrail).
What does the future hold?
In addition to recently launching a fleet management system, Diversey Care has introduced a mobile communication platform called SmartView, which delivers service-performance improvement with a range of real-time management, quality control and reporting features for interdependent cleaning teams in the FM, hospitality and healthcare industries. Its exploration of the role that technology can play in cleaning doesn't stop there, however.
Dr. Ilham Kadri, president of the Diversey Care, says: "We are looking at how hands-free wearable technology such as Google Glass can be adapted to make them useful for the cleaning industry."
Launched in 2013 and now in the hands of a few thousand 'explorers', Google Glass is a wearable computer with an optical head-mounted display (OHMD). Displaying information in a smartphone-like hands-free format, wearers can communicate with the Internet via natural language voice commands.
Kadri adds: "Google Glass could be used to inspect products for reordering purposes or to provide a form of on-site and easily accessible training by, for example, guiding an operative through tasks to help them operate more quickly and efficiently and to make work safer. For example, if a cleaner is unsure how to clean a stain or fix a machine, they could send a picture using Google Glass to head office, who would instruct them through the headset on how to deal with it. Or you could use the technology to take and send a picture of a building to head office to help them provide an estimate for a customer on how much it will cost to clean."
But with one pair of Google Glass glasses currently costing around £890, Diversey Care recognises that it isn't commercially ready.
"We're looking at the iPad and the iPhone as more realistic options at the moment," Kadri continues. "But Google Glass is a peek into what the future could hold. If you look back at the iPhone or GPS satellite navigation systems for your car, they used to be a luxury but now they are affordable."
Company Alpheois has already developed ExpertAtHand, which is said to be the first app for devices like Google Glass that offers the possibility for a cleaning expert to look through the eyes of a cleaner and help and communicate with them in real time. Offering live support, projection of data and message interaction, the app is available both as a service from Alpheios and for cleaning managers themselves to interact with and support their cleaners. With 39.9% of the votes, ExpertAtHand was the winner of the Visitor’s Choice Award 2014 at ISSA/INTERCLEAN Amsterdam 2014.
What the market wants
The science is there to take web-based technology to the next level and beyond but whether it's commercially viable and wanted by the mass market is another matter. Going forward, it will also be interesting to see if cleaning operatives get on board with the technologies that are already available, especially devices that track their productivity, and how easy they find them to use.
SCA president Jan Johansson says: "If you look at this market in general, I think we've been quite slow in adapting new technology into it. But now we're at the stage where we could do lots of new things with digital technology. It's only our imagination which is limiting what we can do and whether the user is prepared to accept them, so now we're waiting to see what the user wants."
Johansson is optimistic about the future, however, and expects to see new opportunities emerge for smart solutions to have a positive impact on the cleaning industry. For instance, he says: "How we monitor and deal with bacteria will become more important the more we travel around – whether that be in a washroom, in an office block or on a hospital ward. So I think we'll see more digital solutions in how to take care of bacteria in public places."
The expression 'knowledge is power' is based on the principle that the more one knows, the more one will be able to control events. Wherever web-based technology leads us, contract cleaners and facilities management companies that adopt these solutions will be hoping that knowledge is profitability too as they face the seemingly impossible challenge to increase quality and decrease costs.
- George Osborne cautious over 50p minimum wage increase
- Cleaning Excellence Conference & Awards is on its way!
- Prime Minister says UK is "past the peak" of Coronavirus cases
- Spring clean: Turning clutter into cash
- Fun on the fairway
- British Airways attacked for lack of cleanliness
- Coronavirus: Experts provide evidence for an app for instant contact tracing
- Mastering commercial cleaning bids
- Coronavirus quarantine rules come into force
- Six crucial spots in your car to clean this summer