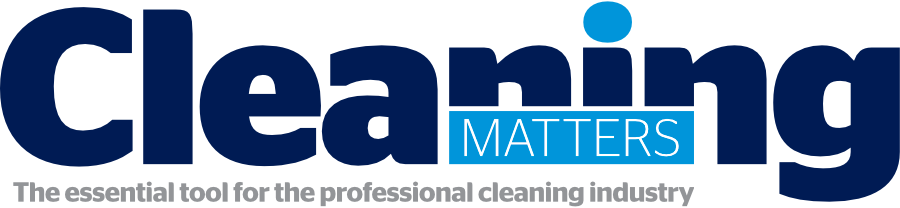
![]() |
Chris Shaw
Editor |
Home> | CONTRACT CLEANING | >Contractors | >Mastering facility maintenance |
Home> | FACILITIES MANAGEMENT | >Infection Control & Prevention | >Mastering facility maintenance |
Home> | CONTRACT CLEANING | >Suppliers | >Mastering facility maintenance |
Mastering facility maintenance
18 May 2023
Whether you are in charge of maintenance for a large facility or are responsible for a cleaning and maintenance company, Matthew Baratta believes creating a detailed outline for operations is crucial for your long-term success.

A CLEANING and maintenance plan promotes cleanliness and safety and can do wonders for the efficiency of time and money spent on maintaining different facilities. A sufficient cleaning and maintenance plan will include an inventory of your equipment, how and when to use it, and best practices so any employee can learn. Making your maintenance plan as comprehensive as possible helps standardise cleaning processes within your facility or company so all employees can maintain compliance, and you can ensure local and regional regulations are met.
Step 1 - Recording inventory: Equipment and chemicals
Knowing your equipment is about much more than just recognising how to turn it on and off. Depending on the scope of your business and operations, the cleaning equipment that you have in your repository can differ significantly. Not all equipment can be used interchangeably, so knowing the ins and outs of your equipment is essential. Luckily, most commercial and industrial-grade cleaning equipment is designed to do the work for you, making them incredibly user-friendly.
Large equipment
Larger equipment such as steam cleaners, carpet extractors, and pressure washers will all come with instructions for when and how to use them. However, sometimes this information can be hard to understand and gets ‘lost in translation’ over time and through changing hands, making it hard to maintain a standard order of operations. Therefore, when you are getting to know a new piece of equipment, take the instructions and synthesise them into digestible steps that can be included in the inventory section of your maintenance plan.
Additionally, take note of the necessary maintenance for different equipment to ensure it keeps running safely and efficiently. Each time you get a new employee, train them on best practices to help ensure your standardised procedure is well understood from the top down.
Chemicals
Another vital component of your cleaning and maintenance inventory is keeping track of the chemicals used and all the precautions that go with them. Using the Globally Harmonized System (GHS) classification system for labelling chemicals is crucial for maintaining compliance.
The system aims to universalise knowledge of hazardous chemicals worldwide. The United Kingdom, the United States and many other countries have adopted the GHS within the regulatory body to ensure more explicit classification and labelling of chemicals.
Understand the labels that designate the chemical's hazardous properties, such as flammability, explosiveness, corrosiveness, or toxicity and store them as necessary. For example, keep flammable materials from heat and ensure proper safety protection for handling coercive and toxic materials. Generally, you never want to mix two cleaning products; having the correct labelling will help avoid this.
Even common household cleaners such as bleach and ammonia can cause lethal chemical reactions when mixed; therefore, labelling and organising your chemicals is the first step in maintaining compliance and safety in your cleaning practices.
Finally, ensure that Safety Data Sheets (SDS) are on file and easily accessible for employees in the event of an accident. Ensure this is up to date with scheduled checks and that other health and safety documentation complies with all applicable regulations.
Understanding what products and equipment should be used on specific surfaces
Steam cleaning
Different surfaces require distinct cleaning methods to be properly disinfected and sanitised– and whether or not chemicals are necessary is a significant factor to consider for commercial and industrial cleaning.
More recently, high-temperature and pressure steam cleaning has become the preferred method for sanitising large areas as it is safer and more environmentally friendly than harsh chemicals. The extremely high-temperature levels are what make steam cleaning effective at killing bacteria without the use of chemicals.
Additionally, the method is versatile, as steam cleaning is compatible with all hard surfaces in commercial and industrial settings. An important factor regarding steam cleaning is that the equipment will require direct contact with the surface to sanitise it effectively. Consequently, you should plan your cleaning accordingly. For cleaning floors, you will want to cover the head of the steam cleaner with a towel to create a steam mop.
When using chemicals on more significant stains, steam cleaners have detergent tanks to safely dispense the product onto the surface. This usually applies to stained upholstery or carpets where the grease and grime cannot be removed with steam and pressure alone. In these cases, it is best to proceed with a non-toxic and environmentally friendly cleaning product that will encapsulate dirt particles and prevent them from re-soiling clean areas.
Pressure washing
For more extensive maintenance tasks such as cleaning heavy-duty equipment, degreasing metal surfaces and floors, and large surface area cleaning in general, a heated pressure washer will be most suitable. A pressure washer is great for large factories and open outdoor spaces that need maintenance, as it is only suitable on surfaces that can handle abundant water at high-pressure levels. These surfaces include the surrounding area, as the splashback from pressure washing can be unpredictable.
Often, the ability for pressure washers to reach high-temperature levels can replace the need for cleaning products or disinfectants in maintenance efforts. However, if you have a large project requiring a disinfecting agent such as bleach, this will not be directly compatible with the pressure washing equipment.
Carpet extracting
As the name suggests, you will need a carpet/upholstery extractor in your toolkit for cleaning large surface areas of the carpet. A commercial or industrial-grade carpet extractor will have a heated steam component alongside low-flow technology to penetrate and remove dirt and grime with little effort. The extractor component is essential here for avoiding re-soiling the carpet or upholstery.
It is critical to consider the material you are working with, as both wool and dyed fabrics will react adversely to the extreme temperature of a carpet steam cleaner. Additionally, when working in industrial facilities, it is essential to consider how long the carpet will take to dry and adjust your cleaning and maintenance plan accordingly. For example, when working in a facility with many different surfaces, consider cleaning the carpets first to give them ample time to dry. However, if you are working in an area where you need to walk on the carpet, you will want to clean it last to avoid bringing bacteria and dirt onto the wet carpet.
When to use chemicals
Chemicals such as quaternary ammonia disinfectants and bleach are frequently used to disinfect surfaces. A sanitising product such as a steam cleaner can kill bacteria on various surfaces; however, disinfectants remain an essential tool.
Arguably, the harshest chemical on the market is bleach, and while it is an effective disinfectant, it is actually less necessary than you may think in regular cleaning practices. Bleach can be extremely harmful if misused and is harsh on the environment when disposed of outside and into water systems. When only sanitising is required, it can be more environmentally conscious to stay away from harsh chemicals.
Using some disinfectants will be essential for maintaining areas such as washrooms and high-touch surfaces in sensitive facilities such as hospitals. However, for cleaning areas such as industrial kitchens, you may opt for a sanitising agent that is not as harsh as disinfectants such as bleach or quaternary ammonia. Food preparation areas should have disinfecting agents to remove potentially harmful contaminations such as salmonella. However, you should always clean and sanitise before disinfecting, as bleach loses its ability to kill germs in the presence of dirt.
Therefore, using a properly registered disinfectant as the last step in cleaning high-touch surfaces in vulnerable facilities will be the best way to maintain compliance and keep the areas free from bacteria and viruses. Always make sure to follow the instructions, especially regarding dwell time to be sure of disinfection.
Strategise your plan of action
The first step in creating a comprehensive plan is to strategise how you will complete your cleaning. Using your inventory of both equipment of chemicals, create a list of surfaces to clean and the corresponding chemicals and equipment you may need. Generally, you will want to clean top to bottom, leaving the floors for last. An exception to this rule is cleaning carpets that need extra dry time – as you may have to add this into your cleaning time. Be wary of the amount of water you use in different areas and account for moving items out of the way, letting the area dry, and then moving them back.
Use the checklist below to help start your strategic plan:
- Using the information above as a guide, create your inventory and apply it room-by-room
- Clean and disinfect all high-touch surfaces: Be sure to use sanitising techniques first, then follow up with chemical components where needed
- Be sure to dust and polish light fixtures, vents and other out-of-reach surfaces that can accumulate dust and affect air quality in the facility
- Proceed with the floors in a motion that requires minimal to no retracing of your steps
- Keep a log of when and who cleaned what. These records will be essential for corporate and public health compliance
- Collect any garbage and disposable cleaning materials to be disposed of at the end of your cleaning.
All in all, maintaining the cleanliness of big facilities can be a daunting task. You want to ensure you use the proper equipment on the right surfaces. Always keep local guidelines for using chemicals and larger equipment in mind, as this will help ensure your maintenance team complies with industry standards. Take the time to detail your inventory and create a strategic plan of action to ensure you start your clean on the right foot.
Matthew Baratta is vice president of operations at Daimer Industries, a specialist technologically advanced commercial and industrial cleaning equipment for major commercial and industrial cleaning and restoration applications. Baratta has extensive cleaning industry knowledge and earned a master’s degree in Public Health.
For more information visit www.daimer.com/
- EHRC looking for evidence of discrimination & exploitation in the cleaning industry
- Cleaning Excellence Awards winners unveiled
- Food premises get a clean sweep
- Supporting the manufacturing sector during winter months
- Registrations open for Cleaning Matters Live
- Guide provides advice on communications with furloughed FM employees
- COVID-19: Prime Minister spends night in ITU
- Oxford scientists develop rapid testing technology for COVID-19
- Room and surface sanitising spray helps prevent coronavirus spread
- Reflections on 2020 and what can we learn?