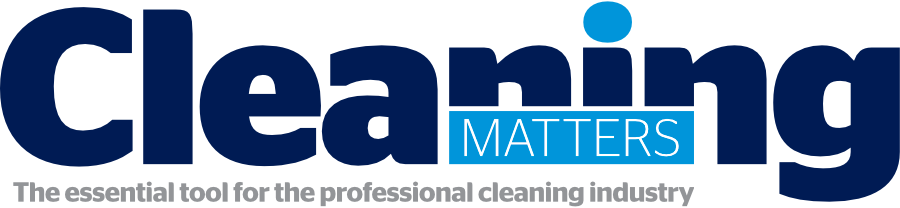
![]() |
Chris Shaw
Editor |
Home> | INDUSTRIAL CLEANING | >High Pressure cleaning | >Delivering under pressure |
Home> | INDUSTRIAL CLEANING | >Pressure Jetters | >Delivering under pressure |
Delivering under pressure
19 April 2017
Richard Geddes, customer accounts manager at Worldwide Cleaning Support, explains how the company created a bespoke pressure washer solution to meet the challenging briefs of two different customers
Have you ever thought of something, anything that you would love to be built specifically for you and only you? Something that you can say is a one of a kind – bespoke maybe. Late last year we had two individual customers come to us with that exact thought. And this is how our twin user bespoke made van mounted 350 bar hot water pressure washer was born. Both unknown to each other were interested in their own versions of the same machine.
Within the UK there are many towns, cities, car parks, footpaths, underpasses - the list could go on - all needing someone to carry out the tasks of cleaning up after - well us! Whether it's that unfinished can of drink you threw in the bin; our name that we once spray painted onto the wall or that pathway that looks a bit grubby next to the playing fields – it all needs cleaning.
Both of our customers said "we need a machine that is mobile but packs a punch; has its own water and power supply; can be used day and night in all weather conditions; can be hot or cold at the flick of a switch; and lets just make it dual user while you’re there". What a good idea, we thought, but how?
The customers added that they "don’t want your average garden jet wash; or anything that needs plugging in". They wanted something that can gently clean a dust bin or bus stop and at the next moment remove stubborn bits of chewing gum from the pavement.
A plan with a van
We thought, why not use a van or a trailer? There is lots of space in either, enough for power and water supply along with a machine that can do everything needed. Both have extra space for chemicals and tools. Both are great options, however a trailer is a bit bulky. Okay a van it is!
Both arrived with their different vans, one long wheel based, one medium. Both customers wanted black plastic flooring for easy cleaning for those expected spillages. Both also went for wooden wall panels giving us options to wall mount items in the future. One van also had a reversing camera installed as standard.
Next we had to decide on what engine, heater and machine to use and how we were going to manufacture it. Roof exhaust or floor exhaust? How do we keep the heat away from the water tanks?
One customer wanted water tanks each side of the van above the wheels to even out the weight; whilst the other wanted their two tanks in the middle of the van. Ultimately the boiler, engine and mounting frame itself had to be in the same place - the rear middle of the van. What about the high pressure hoses, the lances, the attachments, the chemicals? Where are we going to put all of these? Both customers went for a chemical rack behind the cabin, which is easy to access and keep clean; retractable hose reels; door and wall mounted storage.
"I want to work all year round, both day and night – I want lights inside and out and this is a maintenance vehicle people need to see us," one customer said. in response, a pair of spot lights were mounted inside the van but able to shine in or out. One amber flashing light was mounted on the roof for those all-important side-of-the-road jobs.
The test runs went so well that we now have clean patches all across our car park – maybe we need to hire one back. We have had lots of enquiries, some similar, some completely different all with their own bespoke spin. What will we do next?