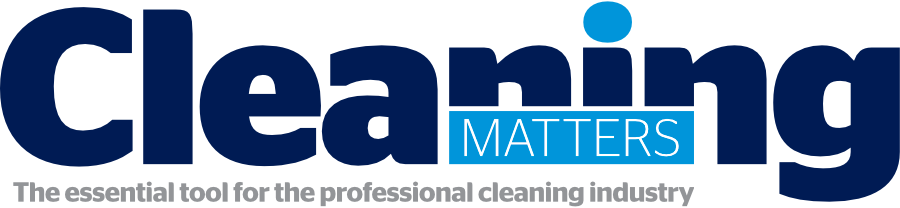
![]() |
Chris Shaw
Editor |
Home> | GENERAL EQUIPMENT & SERVICES | >IT & Software | >Clean with more control |
Home> | GENERAL EQUIPMENT & SERVICES | >Technology & Innovation?Services | >Clean with more control |
Clean with more control
11 July 2016
From robots to augmented reality, Catherine Hackett reports on the latest developments in smart technology for professional cleaning
To say that connectivity is everywhere is an understatement. There are 16 billion devices connected to the internet and that could rise to 30 billion by 2020, according to McKinsey.
Dominating innovation in the cleaning industry, the 'Internet of Things' (IoT) refers to the potential to embed electronics, sensors, actuators and connectivity in everyday objects to make them 'smart'. The purpose is to gather real-time data (from the environment or from the object itself), and/or to perform specific autonomous tasks. This allows for a better delivery of relevant information to the right people at the right time, and for a continual improvement in processes through progressive adjustments.
This 'continual improvement' can translate into higher levels of efficiency, performance and value – as well as increased safety and sustainability, which is important considering that margins in the cleaning service sector remain under pressure as customers demand cost efficiencies and competition increases.
The market is responding with more and more products that incorporate ‘smart’ technology, whether to save on energy and water use, produce real-time data about staff and cleaning-machine fleets, to monitor room occupancy in order to streamline cleaning operations, or to reduce labour-intensive maintenance.
Here come the robots
Cleanfix, which has manufactured robots for many years, won the Innovation Award in the 'Machines, accessories and components' category at ISSA/INTERCLEAN Amsterdam for its latest robotic scrubber dryer: Robot RA 660 NAVI (also known as the Robo 2). It's now in use across Europe due to its ease of use and its ability to scrub and dry vacuum a floor quickly and efficiently using three cleaning brushes (or pads) and a suction unit.
Particularly impressive is its navigation system, which uses patented laser-radar technology that can see 30 metres ahead and pinpoints machine location precisely. There's also its efficiency in mapping rooms, putting in place virtual walls, and its ability to clean to the narrowest of corners. These functions allow the Robo 2 to clean up to 3086m² totally autonomously on one charge, detecting its surroundings and cleaning around obstacles in supermarkets, warehouses, shopping centres and public facilities.
A person is required to fill the machine with water and switch it on. The robot is then controlled using a tablet-style interface, while a SIM cardtracker system connects it to the internet. A rental model is available at £125 a week, while it costs £20,000 to buy the machine outright.
Darren Marston, chairman of Industrial Cleaning Equipment (ICE), which distributes the Robo 2 in the UK, said: "In the past 12 months there has been an emphasis on so many automatic solutions such as driverless cars – and of course on cleaning robots – that people are now starting to believe it will actually happen and the market is now saying we want these things. But using robots are about more than just technology. They're about training staff and maintenance and making a business case."
A new robot from ADLATUS Robotics is designed for professional systematic floor cleaning in supermarkets and public buildings. Fully autonomous, the system consists of the robot itself, which uses sensors to detect and avoid complex obstacles, and a service station where it can recharge its own batteries, pump out waste water and refill its 120 litre tank with fresh water. It can clean 750 to 1500 sqm/h, for two to three-and-a-half hours, with a three-to-eight hour charging time.
Automatic reports produced by the machine are sent to a mobile or Android tablet to show the places that have been cleaned and where it was not possible to clean due to objects. Connectivity with the building is also possible, such as the ability to open and close doors. The machine costs €25,000 and will be on the market by the end of 2016.
The company's Matthias Strobel says robots can "help to overcome the challenges of skills shortages, they can also raise and provide consistent quality, and help with rising personnel costs (such as night- and weekend-shift premiums) as they can work autonomously over long periods including throughout the night."
The first 'Intellibot' robotic machine available from Sealed Air Diversey Care in the UK is the TASKI SWINGOBOT 1650 scrubber drier. Cleaning up to 1000sq.m/hr in a single pass, depending on the number of obstructions, the machine is suitable for education, retail, healthcare and manufacturing applications. The TASKI AEROBOT 1850 vacuum cleaner and the TASKI DUOBOT 1650 will be available later in 2016.
The machines use on-board sensors to complete their pre-programmed floorcare duties with minimal supervision. Diversey Care says that this leaves cleaning operatives to focus on other revenue-generating and value-added tasks, enabling contractors to charge a premium while saving up to 80% on labour costs. Its Eco Save filtration system also means that the scrubbers use up to 85% less water and chemistry per eight-hour shift than traditional manual scrubbers.
Intellibot machines are fitted with Intelli-Trak – a remote monitoring system where communication both to and from the robot makes it possible to report remotely on utilisation performance. It is also possible to remotely perform diagnostics, which help prevent or reduce machine downtime.
Augmented Reality
Both the Intellibot machines and Intelli-Trak system are part of Diversey's 'Internet of Clean' (IoC) – an IOT ecosystem that connects its machines, dispensers, sensors, beacons and other smart devices, enabling businesses to monitor their operation remotely.
Another device connected to this platform is Suma Revoflow. An Augmented Reality (AR) app for use with this dispensing system won the ‘Management, Training Solutions and Related Products’ category and the overall award at the ISSA/INTERCLEAN Innovation Award.
The app enables the user to self-train, self-troubleshoot and receive remote support directly from Diversey Care through a mobile phone or tablet. The cleaning operative points the camera view on their mobile device at the equipment, the object is recognised and digital guidance is provided in real time with a life size overlay on the device. This is said to reduce downtime, improve cost efficiency and operational consistency, while up-skilling employees without the need for previous training.
According to Dr. Ilham Kadri, president of Diversey Care, providing cleaning operatives with new technology not only helps to tackle the problems associated with the industry’s high employee turnover – training, knowledge transfer, development of skills and reduction of errors – but can also reduce employee turnover by increasing job satisfaction.
"No one dreams of becoming a cleaner," she says. "There is a high turnover because they leave as soon as they find a better job. But one of the cleaning operatives who trialled the TASKI Intellibot robot said to me, 'The day I had a robot with me I felt so empowered'. Digital knowledge solutions support this by helping them to get the right information at the right point of time, which encourages them to stay and climb the ladder in the cleaning industry."
Sensing a change
Key to the IoT is the Wireless Sensor Network: a low cost and lightweight network, made up of sensors with low energy requirements. An industrial sensor can be placed in a range of equipment – from a dishwasher, tap or soap dispenser to a chemical dosing system – connecting it to the internet. From here, real-time data on its usage is fed into the cloud, from where it can be analysed.
New bluetooth-enabled air dryers from Ffuss detect information such as the number of drying cycles that have taken place, the total working time and the number of hours the unit has been plugged in. This information can be viewed on a smartphone or tablet to anticipate maintenance needs. Ophardt has also launched a smart tap that uses bluetooth technology to provide water and soap, as well as disinfectant for automatic cleaning of the sink. It is said to use less water, and the amount of soap to be dispensed can be programmed.
To enable managers to monitor traffic and usage in the washroom, SCA has connected a number of smart dispensers through its Tork Easycube system. This means cleaning can be carried out when and where it’s needed – not around a fixed schedule. The system will launch in the UK later this year.
SCA's communications manager Jamie Wright said: "Only approximately 4% of costs are washroom products so shaving 10p off the price of toilet tissue won't make a big difference to a company's bottom line. But if you make cleaning operatives more efficient so that they don't have to revisit the washroom to check dispensers that don't need refilling, you can reduce the massive 80% of costs spent on labour to provide bigger benefits to the cleaning provider."
The next step could be using smart technology to influence user behaviour such as proper hand washing. Deb is already trialling The DebMed Group Monitoring System (GMS) in six hospitals in the UK, where it will officially launch later this year. The system uses a wireless network of dispensers to detect every hand cleaning action as it occurs. This information is sent to a DebMed server where DebMed GMS calculates compliance against a scientifically-valid algorithm. This takes into account the conditions of each hospital unit, such as census and nurse-to-patient ratio, to accurately predict the expected hand hygiene opportunities, within the facilities ever-changing conditions.
"When you only have a visual reporting tool, 95% of hospitals are in denial about the hand hygiene figures," Deb's marketing manager Paul Jakeway says. "This goes down to 30-40% when they are presented with hard facts and figures from DebMed. We are then in a better position to ask how can we help them."
Intelligent buildings
Solutions from FacilityApps allow contract cleaners to digitally manage their mobile workforce throughout an entire building by means of apps on a smartphone or tablet.
Chief IoT officer a.i. Jorus Everaerd says: "Our solution helps you see how people are spread in your building, how many people used the washroom and how full waste bins and towel dispensers are. You get real-time information, you can analyse usage, optimise processes and take action to improve service levels and staff efficiency."
The 'Binster' waste bin contains a sensor to measure how full it is in realtime, so the cleaning operative knows whether it needs refilling or not. According to Evidence Based Cleaning, clients have indicated savings on personnel costs of up to 25%, with improvements in service levels. The company also provides sensors in washrooms and ‘live trolley tracking’.
‘iBeacon’ technology makes indoor navigation possible by creating a 50 metre zone. When a member of staff enters the different zones with the app a message is sent to the company to register their time and/or to provide proof that they were in a certain area. ‘Wifi-tracking’ shows how busy it is in certain zones in a building by measuring all the wifi devices in a building. This information can be translated into the work schedules of cleaning staff.
Karcher's 'Connected Cleaning' concept, is also focused on digitising building cleaning. The first element is Kärcher Fleet: a fleet management system based on the installation of a mobile communications unit in the cleaning machine. It sends machine data – from localisation to operating times, battery status and maintenance status – to an online customer portal, where a graph of the data is provided. Using this information, the facility manager can, for example, increase machine utilisation or reduce downtimes. The second element – Kärcher Manage – allows cleaning processes to be recorded with a barcode scanner, determining the time spent on any room to which specific cleaning activities have been assigned. This is useful for the final costing of contracts and for the preparation of new quotes.
Dr Friedrich Völker, head of digital products at Kärcher, said: "With Connected Cleaning, we are laying the foundation for utilising future developments in building digitalisation for the efficient execution of cleaning tasks. If, for example, the lift reports the number of people on each floor, or a certain vending machine is used particularly frequently, cleaning can be performed based on need rather than a rigid cleaning plan."
Smart technology isn't going anywhere, according to experts. In fact Vincent Everts, a professional trend watcher, says: "In three years, it will become essential to know how to use modern technology to be competitive." But ultimately, the data captured and analysed by smart technology is of little value unless businesses act on it. Likewise, it is up to decision makers to drive engagement within their individual organisations, ensuring staff are not only trained but motivated to work with robots or use cutting-edge support tools.
- Six crucial spots in your car to clean this summer
- UK company launches household cleaner that destroys COVID-19 in 60 seconds
- Reformulated organic drain clearer unveiled
- Rats invade Paris
- New COVID-19 vaccine prevents 90% of infections
- Clock is ticking for waste criminals as new taskforce launched
- WCEC becomes first livery company to be accredited as Living Wage employer
- WHO: Coronavirus airborne transmission cannot be ruled out
- Have your say on the future of cleaning & hygiene
- BOHS expresses 'apprehension' about WHO's COVID-19 findings