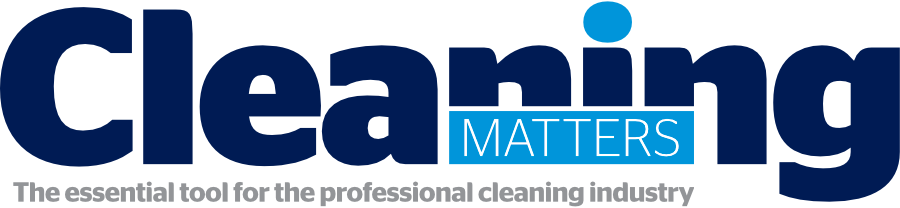
![]() |
Chris Shaw
Editor |
Home> | CONTRACT CLEANING | >Contractors | >Rubbermaid at Heathrow airport |
ARTICLE
Rubbermaid at Heathrow airport
11 November 2015
Opened in March 2008, Heathrow Terminal 5 (T5) adds capacity to Heathrow airport, allowing an extra 30 million passengers to travel through Europe's busiest airport every year and increasing the annual passenger total to 90 million.
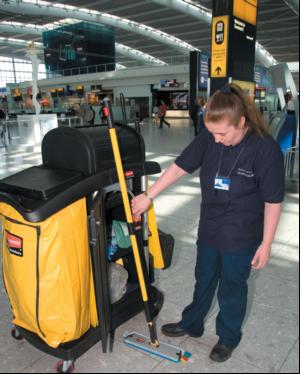
Costing £4.3 billion, the terminal building is the UK's largest
freestanding structure, comprising 3.8 million square foot of space spread
across four floors.The building is in use 24 hours a day, so when building
services contractor Amey was awarded the cleaning and maintenance
contract for T5, it needed to create a robust cleaning process that could
ensure the highest cleaning standards in a large building.
Amey is one of the UK's leading support service contractors for both the public and private sectors,employing more than 10,000 people in over 200 locations across the country. Amey works with clients from the aviation, central government, defence, education, local government, rail and strategic highways markets.
Unique Challenges As the UK's new flagship airport terminal,Terminal 5 needed a world-class cleaning solution to maintain a clean, safe environment for travellers.
Pedro Gomez, Soft Services Manager for Amey, explains how Amey's work within the building is categorised:"Our remit extends to both hard and soft services. I oversee the soft services section, dealing with everything from day-to-day cleaning to security and compliance issues." Heathrow Terminal 5 is a showcase project for UK airport operator BAA.As such, BAA have set high standards for the work carried out by Amey, including regular quality assessments and incentives for outstanding results."BAA naturally wants to ensure the very highest standards at T5"says Gomez,"so we needed the best equipment to help us achieve and maintain our great service." Amey were awarded the contract at the start of 2010, so Gomez and his team needed durable cleaning products that maximised productivity for his staff."We have 400 cleaning personnel here at T5, and from the outset we required a lot of efficient and reliable cleaning equipment. Being an airport,we have some very particular challenges.We have to adapt on a daily - and often hourly - basis to the number of passengers coming through the airport, whilst security is always a paramount concern."
The Rubbermaid Solution Amey had been aware of Rubbermaid's successes at similar locations, such as Southampton Airport, and had previous positive experiences of using Rubbermaid's products with past projects.
Amey chose Rubbermaid's HYGENâ„¢ microfibre cleaning system as a key part of their cleaning services plan.HYGENâ„¢ is a total solution featuring a complete set of textiles and hardware products, such as handles, frames, buckets and carts, designed to maximise the benefits of microfibre cleaning.
In particular, three major items influenced Amey's choice: Rubbermaid secure cleaning carts,Rubbermaid Pulse kit and highlevel dusting tools.
The secure cleaning carts are equipped with light, hard-wearing equipment that enable the cleaning staff to move around the large building at speed and with minimal disruption to passengers and airport staff.
The choice of Rubbermaid's Pulse kit with microfibre mop pads is consistent with T5's sustainability standards, minimising the environmental impact without any loss of productivity.
Finally,with its wide open spaces, hardfloors and hard-to-reach signage, the majority of T5's cleaning tasks involve dusting floors and dusting higher surfaces. Crucially, the Rubbermaid dusting equipment is supplied with extension poles for high-level dusting, and the dust pads can be easily re-shaped to reach awkward positions.All Rubbermaid products were supplied through Amey's existing janitorial and disposable products distributor, Bunzl Cleaning and Hygiene Supplies (BCHS).
The Benefits Rubbermaid's HYGENâ„¢ system brought a series of benefits to Heathrow Terminal 5:
Improved Efficiency Being at the mercy of passenger footfall through the terminal (regularly exceeding 30,000 passengers each day), Gomez and his team perform deep cleans during the night when the terminal is less crowded."Once we have established a good standard of cleanliness on the night shifts, we then look to maintain that during the day, with less intensive and less intrusive preventative cleaning duties." Rubbermaid's products have helped Gomez increase the efficiency of these daytime cleaning 'top-ups'by supplying wide microfibre dust mops and easily manoeuvrable cleaning carts.The HYGENâ„¢ Microfibre mop makes fast work of general hardfloor dusting, and the microfibre pads are easily removed and replaced by the cleaning staff.The pads are guaranteed machine washable for over 500 launders without degradation.
Rubbermaid's Pulse Mop allows the user to apply three streams of water directly onto the surface, thereby eliminating the time taken to return to a mop bucket for water refills.All the above cleaning products can be transported on a single HYGENâ„¢ Cleaning Cart, giving the user everything they need to tackle any cleaning job.
Reduction in Water Usage "Rubbermaid's microfibre mops and cloths mean we are using less water"says Gomez."Microfibre is very effective at removing dirt with minimal quantities of water. In fact,we rarely use any chemicals in day-today cleaning." "Microfibre is proven to reduce water usage by 80%, and chemical consumption by anything up to 95%"adds Rubbermaid's Rob Sutherland.
Gomez notes how these advantages fit perfectly with T5's sustainability aims:"Terminal 5 has two water systems: one fresh water mains supply and a second 'grey water' recovery that uses water collected from the roof.
Any method of cutting water use is a major advantage."
A Safer Environment Microfibre also brings other benefits."We are cleaning a wide range of items and surfaces"says Gomez,"including train platforms, escalators and electronic equipment - any excess water could potentially be hazardous around these areas." A surface cleaned with a damp microfibre mop pad dries in about 90 seconds,whereas a standard cotton string-style mop could take upwards of 10 minutes.The faster drying speed of microfibre helps to significantly reduce slip-hazard areas for passengers and staff, and to reduce the amount of time each section of floor needs to be out of use for cleaning.
Also,Rubbermaid's secure cleaning carts contribute to increasing security throughout the airport.Their lockable compartments are crucial when transporting hazardous cleaning chemicals around an air terminal.
Style and Productivity Thanks to Rubbermaid's trademark stylish designs,Gomez describes the Rubbermaid products as a 'good fit' for the terminal:"T5 is a modern building, and Rubbermaid's product line is at the same time efficient and a good aesthetic match." However, it is not a case of style over substance."We have been very happy with the gains achieved since using Rubbermaid products.Overall, we believe we have increased productivity by 15 - 20%."adds Gomez.
This improvement means passengers are better served by the Terminal's facilities, and preventative cleaning tasks are made easier with Rubbermaid's lighter,more convenient tools.This also makes them popular with the cleaning staff at T5.
Strong Understanding of Customers Rubbermaid strives to understand the needs of each client and identify the particular challenges of each scenario.Rob Sutherland, Business Development Manager for Rubbermaid in the UK, points to the precedent set by Amey and Rubbermaid's partnership at T5:"With T5, Amey and Rubbermaid have led the way in modern airport cleaning techniques,and we know that other airports are looking to this as a perfect example of how to implement a large scale cleaning project." Rob Sutherland's recommendations for which products to use at T5 were based on a consultative approach,working with Gomez's team to select the optimal combination of cleaning tools."When the relationship is good and communication is good,"says Sutherland,"it is easy to find the very best solution." "We have been impressed by the level of after-sales support,"says Gomez."Rubbermaid representatives were here every day giving us tips on how to get the best out of each product.We would certainly recommend Rubbermaid Commercial Products in the future."
Conclusion Amey chose Rubbermaid's HYGENâ„¢ Microfibre Cleaning System as a total solution for Heathrow Terminal 5.Three items were particularly important for meeting the unique challenges set by the T5 project: secure cleaning carts,Rubbermaid Pulse kit and high-level dusting tools.
There have been many tangible benefits from the introduction of Rubbermaid cleaning products.The lockable carts are an advantage in high security areas,proving to be fundamental when transporting hazardous cleaning chemicals.Rubbermaid Pulse and microfibre mops dramatically reduce the amount of water used, eliminating the time taken to return to a mop bucket for water refills and bringing substantial environmental benefits.The lightweight designs of the Rubbermaid products help to reduce user fatigue and speed-up common tasks.
Thanks to the introduction of Rubbermaid cleaning equipment, productivity has increased by 15-20%.Working closely with Amey, Rubbermaid was able to provide the best possible cleaning solution, which perfectly fitted the unique requirements of T5.
Amey is one of the UK's leading support service contractors for both the public and private sectors,employing more than 10,000 people in over 200 locations across the country. Amey works with clients from the aviation, central government, defence, education, local government, rail and strategic highways markets.
Unique Challenges As the UK's new flagship airport terminal,Terminal 5 needed a world-class cleaning solution to maintain a clean, safe environment for travellers.
Pedro Gomez, Soft Services Manager for Amey, explains how Amey's work within the building is categorised:"Our remit extends to both hard and soft services. I oversee the soft services section, dealing with everything from day-to-day cleaning to security and compliance issues." Heathrow Terminal 5 is a showcase project for UK airport operator BAA.As such, BAA have set high standards for the work carried out by Amey, including regular quality assessments and incentives for outstanding results."BAA naturally wants to ensure the very highest standards at T5"says Gomez,"so we needed the best equipment to help us achieve and maintain our great service." Amey were awarded the contract at the start of 2010, so Gomez and his team needed durable cleaning products that maximised productivity for his staff."We have 400 cleaning personnel here at T5, and from the outset we required a lot of efficient and reliable cleaning equipment. Being an airport,we have some very particular challenges.We have to adapt on a daily - and often hourly - basis to the number of passengers coming through the airport, whilst security is always a paramount concern."
The Rubbermaid Solution Amey had been aware of Rubbermaid's successes at similar locations, such as Southampton Airport, and had previous positive experiences of using Rubbermaid's products with past projects.
Amey chose Rubbermaid's HYGENâ„¢ microfibre cleaning system as a key part of their cleaning services plan.HYGENâ„¢ is a total solution featuring a complete set of textiles and hardware products, such as handles, frames, buckets and carts, designed to maximise the benefits of microfibre cleaning.
In particular, three major items influenced Amey's choice: Rubbermaid secure cleaning carts,Rubbermaid Pulse kit and highlevel dusting tools.
The secure cleaning carts are equipped with light, hard-wearing equipment that enable the cleaning staff to move around the large building at speed and with minimal disruption to passengers and airport staff.
The choice of Rubbermaid's Pulse kit with microfibre mop pads is consistent with T5's sustainability standards, minimising the environmental impact without any loss of productivity.
Finally,with its wide open spaces, hardfloors and hard-to-reach signage, the majority of T5's cleaning tasks involve dusting floors and dusting higher surfaces. Crucially, the Rubbermaid dusting equipment is supplied with extension poles for high-level dusting, and the dust pads can be easily re-shaped to reach awkward positions.All Rubbermaid products were supplied through Amey's existing janitorial and disposable products distributor, Bunzl Cleaning and Hygiene Supplies (BCHS).
The Benefits Rubbermaid's HYGENâ„¢ system brought a series of benefits to Heathrow Terminal 5:
Improved Efficiency Being at the mercy of passenger footfall through the terminal (regularly exceeding 30,000 passengers each day), Gomez and his team perform deep cleans during the night when the terminal is less crowded."Once we have established a good standard of cleanliness on the night shifts, we then look to maintain that during the day, with less intensive and less intrusive preventative cleaning duties." Rubbermaid's products have helped Gomez increase the efficiency of these daytime cleaning 'top-ups'by supplying wide microfibre dust mops and easily manoeuvrable cleaning carts.The HYGENâ„¢ Microfibre mop makes fast work of general hardfloor dusting, and the microfibre pads are easily removed and replaced by the cleaning staff.The pads are guaranteed machine washable for over 500 launders without degradation.
Rubbermaid's Pulse Mop allows the user to apply three streams of water directly onto the surface, thereby eliminating the time taken to return to a mop bucket for water refills.All the above cleaning products can be transported on a single HYGENâ„¢ Cleaning Cart, giving the user everything they need to tackle any cleaning job.
Reduction in Water Usage "Rubbermaid's microfibre mops and cloths mean we are using less water"says Gomez."Microfibre is very effective at removing dirt with minimal quantities of water. In fact,we rarely use any chemicals in day-today cleaning." "Microfibre is proven to reduce water usage by 80%, and chemical consumption by anything up to 95%"adds Rubbermaid's Rob Sutherland.
Gomez notes how these advantages fit perfectly with T5's sustainability aims:"Terminal 5 has two water systems: one fresh water mains supply and a second 'grey water' recovery that uses water collected from the roof.
Any method of cutting water use is a major advantage."
A Safer Environment Microfibre also brings other benefits."We are cleaning a wide range of items and surfaces"says Gomez,"including train platforms, escalators and electronic equipment - any excess water could potentially be hazardous around these areas." A surface cleaned with a damp microfibre mop pad dries in about 90 seconds,whereas a standard cotton string-style mop could take upwards of 10 minutes.The faster drying speed of microfibre helps to significantly reduce slip-hazard areas for passengers and staff, and to reduce the amount of time each section of floor needs to be out of use for cleaning.
Also,Rubbermaid's secure cleaning carts contribute to increasing security throughout the airport.Their lockable compartments are crucial when transporting hazardous cleaning chemicals around an air terminal.
Style and Productivity Thanks to Rubbermaid's trademark stylish designs,Gomez describes the Rubbermaid products as a 'good fit' for the terminal:"T5 is a modern building, and Rubbermaid's product line is at the same time efficient and a good aesthetic match." However, it is not a case of style over substance."We have been very happy with the gains achieved since using Rubbermaid products.Overall, we believe we have increased productivity by 15 - 20%."adds Gomez.
This improvement means passengers are better served by the Terminal's facilities, and preventative cleaning tasks are made easier with Rubbermaid's lighter,more convenient tools.This also makes them popular with the cleaning staff at T5.
Strong Understanding of Customers Rubbermaid strives to understand the needs of each client and identify the particular challenges of each scenario.Rob Sutherland, Business Development Manager for Rubbermaid in the UK, points to the precedent set by Amey and Rubbermaid's partnership at T5:"With T5, Amey and Rubbermaid have led the way in modern airport cleaning techniques,and we know that other airports are looking to this as a perfect example of how to implement a large scale cleaning project." Rob Sutherland's recommendations for which products to use at T5 were based on a consultative approach,working with Gomez's team to select the optimal combination of cleaning tools."When the relationship is good and communication is good,"says Sutherland,"it is easy to find the very best solution." "We have been impressed by the level of after-sales support,"says Gomez."Rubbermaid representatives were here every day giving us tips on how to get the best out of each product.We would certainly recommend Rubbermaid Commercial Products in the future."
Conclusion Amey chose Rubbermaid's HYGENâ„¢ Microfibre Cleaning System as a total solution for Heathrow Terminal 5.Three items were particularly important for meeting the unique challenges set by the T5 project: secure cleaning carts,Rubbermaid Pulse kit and high-level dusting tools.
There have been many tangible benefits from the introduction of Rubbermaid cleaning products.The lockable carts are an advantage in high security areas,proving to be fundamental when transporting hazardous cleaning chemicals.Rubbermaid Pulse and microfibre mops dramatically reduce the amount of water used, eliminating the time taken to return to a mop bucket for water refills and bringing substantial environmental benefits.The lightweight designs of the Rubbermaid products help to reduce user fatigue and speed-up common tasks.
Thanks to the introduction of Rubbermaid cleaning equipment, productivity has increased by 15-20%.Working closely with Amey, Rubbermaid was able to provide the best possible cleaning solution, which perfectly fitted the unique requirements of T5.
MORE FROM THIS COMPANY
OTHER ARTICLES IN THIS SECTION