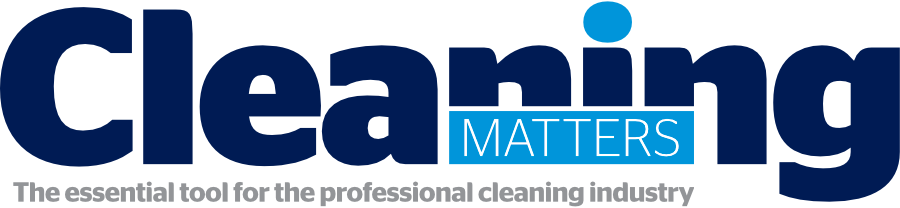
![]() |
Chris Shaw
Editor |
Home> | SUSTAINABILITY | >Energy Efficiency | >Compliance, cleanliness and safety |
Home> | SUSTAINABILITY | >Green Cleaning Methods | >Compliance, cleanliness and safety |
Home> | FACILITIES MANAGEMENT | >Infection Control & Prevention | >Compliance, cleanliness and safety |
Compliance, cleanliness and safety
26 July 2022
THE IMPORTANCE of compliance, cleanliness and safety in industrial workplaces is critical according to MEWA UK country manager, Günes Yenen.

Yenen believes looking at how something as simple as the choice of cleaning wipes can improve hazardous waste management. A clean working environment plays a key role in ensuring productivity, quality assurance and employee wellbeing and satisfaction. A wide range of fluids, such as oil, other lubricants and hydraulic fluids, are employed in industrial environments and leaks and spills onto floors and surfaces are therefore a regular occurrence. This can create further issues as workers tread in the spillage and spread the liquid into other areas. Keeping such areas clean, safe and compliant is a balancing act.
Health, safety & compliance
Ill health and work-related injuries cost the British economy £16.2billion over 2019-2020. Every year thousands of accidents and cases of ill health are reported from activities at industrial and commercial facilities and Health and Safety Executive (HSE) figures show that slips, trips and falls are the most common workplace injuries accounting for 33%. These may sound relatively innocuous but can result in serious injuries meaning long absences for employees affected. Another significant source of ill health in industrial settings can arise from exposure to hazardous materials such as metalworking fluids, solvents and degreasers, as well as additives and contaminants such as metal fines. These can affect skin and respiratory health, with common occupational diseases associated with such hazardous materials including dermatitis and asthma.
Employers are typically required to ensure, as far as is reasonably practicable, the health and safety of all employees as mandated by the Health and Safety at Work Act. Companies must assess any potential risks to the health and safety of employees and others and take appropriate action to put effective control measures in place.
Companies which fail to prioritise workplace safety could face significant reputational and commercial risks. The HSE is responsible for regulatory enforcement that can see substantial fines, and in extreme cases prison, levied on companies and their directors.
Measures required under the Act include taking steps to control slip and trip risks as well as exposure to hazardous materials. Specific recommendations are to keep absorbent materials to hand where there is a risk of a spillage and to clean up spills promptly to minimise the risk of exposure and slips and trips.
This sounds straightforward, however, it can potentially generate additional challenges. Manufacturing companies typically use blue paper roll or single use rags to absorb and mop up spilled liquids or clean machine parts. However, any blue roll or rags which are used for this application then potentially become classed as hazardous waste which then requires suitable management and disposal.
To ensure compliance with legal regulations, businesses producing hazardous waste in the UK - including wipes used to mop up spillages - have a specific ‘duty of care’ concerning that waste and must classify, separate and store any waste safely before it is disposed of by an authorised hazardous wastes contractor.
Storing contaminated wipes
Contaminated wipes may emit volatile organic compounds (VOCs) or pose a fire risk, depending on the fluid they have been used to wipe up. To minimise risk to worker health and safety, they should be stored in a tightly closable container made of resistant material such as metal or special plastic (high-molecular, low-pressure polyethylene) before being disposed of in the correct way.
New options
With companies facing increased pressure to attain high standards of health and safety, the practice of an alternative strategy to disposable paper towels and rags has emerged.
Today, full-service contract third-party suppliers are delivering high quality reusable absorbent industrial wipes to customers, along with robust storage containers that keep contaminated wipes safe and legally compliant until collection. The reusable service system also removes the significant burden of hazardous waste disposal from the company, reducing overall costs as well as mitigating potential health and safety fines. And because the wipes are delivered on a pre-agreed rotation, they are always to hand, so spills can be rapidly addressed to reduce the risks of exposure to chemicals and slipping causing injury.
Environmental benefits
Not only do such services simplify cleaning and waste management, they are also more environmentally friendly than conventional alternatives. The wipes can be re-used up to 50 times and, at MEWA, we estimate that the adoption of this service by our customers prevents some 85,000 tonnes of industrial waste being created.
Even small changes to a typical maintenance regime in plant and manufacturing facilities can yield considerable benefits helping to protect employee health and well-being, aiding regulation compliance and reducing your environmental impact.
Günes Yenen is UK country manager at MEWA UK.
For more information visit www.mewa.co.uk
- Chemical free attraction
- More water efficient scrubber dryers on ECA scheme
- Council cleaners go bleach free to green up Liverpool
- Green at source
- Scheme saves water, saves money, saves tax
- Ioning out chemicals in cleaning
- Wipe out waste with contaminated wipes laundry service
- Companies partner for green paper drive
- Good reaction to environmental best practice awar
- A cool half