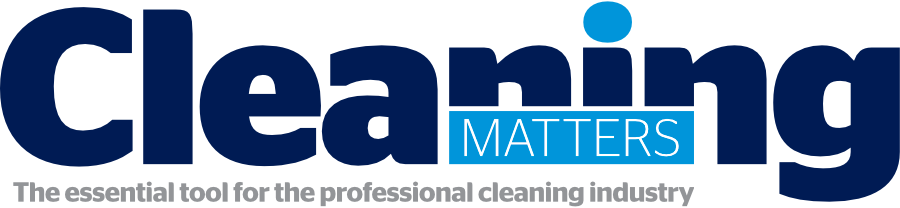
![]() |
Chris Shaw
Editor |
Home> | Events | >Facilities Matters | >Maintenance operatives and workplace exposure |
Home> | FACILITIES MANAGEMENT | >Security | >Maintenance operatives and workplace exposure |
Maintenance operatives and workplace exposure
29 October 2020
WITH THE potential to be exposed to the highest levels and widest range of harmful physical and chemical agents, Chris Mills examines why maintenance operatives must be monitored closely to ensure that they remain fully compliant with the appropriate health and safety legislation, guidelines and limits.
Occupational hygiene consultants visit a wide range of industries, from bakeries and petroleum plants to pharmaceutical sites and foundries. In addition to production operatives, many sites also employ maintenance operatives. This group of workers often have the potential to be exposed to the highest levels and widest range of harmful physical and chemical agents in a workplace, and as a result, must be monitored closely to ensure they remain fully compliant with the appropriate health and safety legislation, guidelines and limits.
What is a maintenance operative?
The role of a maintenance operative (or fitter) can vary greatly from site to site. At smaller companies, the maintenance operative covers a wide range of responsibilities, carrying out genuine maintenance, looking at breakdowns, repairs and fabrication and painting and cleaning up where necessary. Smaller companies will sometimes have just one maintenance operative, whereas larger companies may have teams who cover different shifts. These may be dedicated to either electrical or engineering works, or just have their own areas of large sites to cover.
Why is it so important to regularly monitor a maintenance operative’s exposure to hazardous substances?
When it comes to monitoring exposure to airborne substances which are hazardous to health, a maintenance operative can potentially visit any area of the site and be involved in multiple activities and processes in any given day. Maintenance operatives will usually be exposed to whatever substances are present in the area that they are sent to work in; however, fitters can also create additional airborne substances, such as dust from grinding/drilling, fume and gases from welding and cutting and solvent vapours from the use of sprays, adhesives and paints. They may also have to clean down the area they are visiting prior to any work being carried out, as this could lead to secondary dust exposures if the area is not cleaned thoroughly.
Fitters will often also carry out a wide range of maintenance work and repairs within their own workshops. In many cases, no two days will be the same in terms of location, duration and tasks carried out by maintenance staff, and therefore they can be exposed to differing substances at varying levels of exposure, producing a number of different exposure results throughout the week. One day’s sampling is unlikely to be representative of ‘typical’ exposure, and therefore monitoring across a range of activities should be considered for these types of workers. Where possible, exposure monitoring should be aligned with maintenance schedules to capture and assess specific tasks.
In addition to these difficulties in assessing a fitter’s exposure, the method of monitoring may be restricted due to the area they are working in. For example, work may be within a confined space, and as a result, the operative may be unable to wear a sampling train. In DSEAR areas, ATEX rated equipment will be required in order to prevent explosions. In food industries, glass instruments and sample media might not be appropriate due to the risk of contaminating the products. Sampling equipment may also need to be specially cleaned in food/pharma environments.
Before carrying out any monitoring, occupational hygiene consultants will need to know the areas that the operative may be visiting and what they are monitoring the maintenance operative for. This of course may change if they are called out for an emergency maintenance job in another area of the site. Once the maintenance work has been carried out, further consideration should be taken as to what the results are representative of and if this has varied from the initial scope.
How do you monitor a maintenance operative according to the substance they are exposed to?
Noise
When monitoring a maintenance operative for noise, their exposure is likely to be different every day. Exposure levels are generally down to the areas they visit, whether or not the plant is running in the areas they are working and the tools they have to use. Short periods of very high intensity noise generated by power tool use or hammering can have a significant effect on an operative’s daily noise exposure. This can be overlooked in a task risk assessment and, as a result, inadequate controls are put in place. Many potential sources of exposure should be considered during an assessment, which may involve short-term samples of multiple scenarios to enable maintenance teams to minimise their exposure.
Upon entering Hearing Protection Zones, maintenance operatives must wear hearing protection, especially if machinery is running. However, if the machinery is not running, a maintenance operative may decide that hearing protection is not required. They should still be mindful that the use of power tools can create high noise levels. Fitters should be supplied with sufficient information regarding the noise levels of specific tools and the effect of their own exposure, as well how much it would impact those around them. This information will allow for the correct selection of hearing protection as and where appropriate.
Vibration
Many of the tools used by a maintenance operative – including impact wrenches, drills, grinders and saws – will lead to hand arm vibration exposure. The specific tools that are used, the duration of use and the manner in which they are used is likely to vary from day-to-day. As a result, assessment of exposure to hand arm vibration will be required daily.
It is recommended that all tools with their various attachments are measured for typical vibration levels, and the number of HSE vibration points per five/ten minutes is calculated. Maintenance operatives should then have the list of tools and points with them so as to be able to calculate their likely exposure during their working day. Once the Exposure Action Value of 100 points is reached, no further use of vibrating tools should be undertaken. This may prove difficult where the maintenance team is a ‘one man band’; however, it is important to give these operatives the required information to assess whether or not a task can be completed by a single member of staff.
EMF
Maintenance operatives may also be exposed to the unintentional emission of electromagnetic fields (EMF) from electrical equipment, including welding sets, battery and electric power tools and electrical plant equipment they may be working on. In most cases, it will be possible to assess the risk of exposure by using HSE guidance, manufacturer’s details and other resources, such as those provided by the Welding Institute. A key control for maintenance operatives during welding would be to avoid draping welding cables over their body, as this is typically where the most significant exposures will arise. EMF from welding equipment and power tools poses a far greater risk to health to ‘employees at particular risk’, including those with active implants, such as pace makers. Therefore, an additional risk assessment would need to be generated, which may include the requirement to measure EMF with specialist equipment. Additional controls, such as signage, restricting access and use of certain equipment, would also need to be applied.
In summary, a maintenance operative is commonly exposed to the highest levels and widest range of substances and physical agents at work. However, exposure to workplace hazards can sometimes be overlooked, with monitoring often considered as an afterthought. Careful consideration should be taken towards a wide range of maintenance worker tasks prior to their taking place, as this will ensure the most appropriate exposure control measures can be applied. This may involve the specific measurement/assessment as carried out by a qualified occupational hygienist, or the use of known concentrations or levels for given tasks.
SOCOTEC’s occupational hygiene team is fully equipped to provide organisations of all sizes and sectors with the knowledge required to assess and control the level of risk in their workplace, including workplace exposure monitoring and occupational noise assessments.
Chris Mills is occupational hygienist at SOCOTEC UK
For more information visit www.socotec.co.uk
- Security acquisition
- Combined cleaning & security
- Light at the end of the tunnel
- Get to grips with gritting
- Top marks for security services
- Multi-service contract with industrial components supplier
- Axis Group sponsors Sage Gateshead
- Cutting-edge contract cleaning
- Trigion deal with Domino UK is no game
- Cleaning and security services