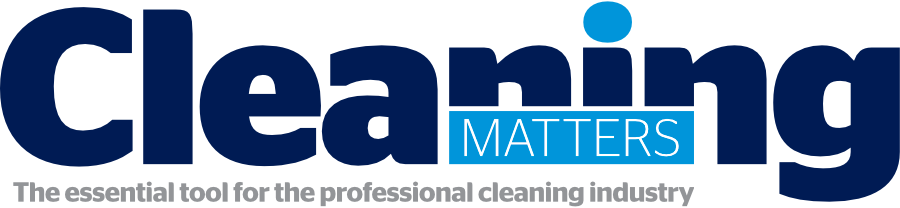
![]() |
Chris Shaw
Editor |
Home> | INDUSTRIAL CLEANING | >High Pressure cleaning | >Management of effluent and discharge in railway depots |
Home> | INDUSTRIAL CLEANING | >Industrial Cleaning machines | >Management of effluent and discharge in railway depots |
Home> | INDUSTRIAL CLEANING | >Industrial Equipment & Services | >Management of effluent and discharge in railway depots |
Management of effluent and discharge in railway depots
20 April 2021
Emily Hill asks how organisations can remain compliant when it comes to managing the quantity and quality of effluent produced by railway traction and at rolling stock maintenance depots.
FROM CLEANING train exteriors/shed inspection pits to filling toilet tanks on carriages, water fulfils a host of different functions in order to keep the rail industry operating. Once used, water is almost always returned to the environment in the form of effluent discharges and waste, either to the foul sewer system managed by the local water utility company or to controlled sources such as rivers and streams.
Trade effluent and wastewater discharge can be a costly necessity which, if not monitored and managed correctly, can have a detrimental impact on the environment, as well as having severe legal and financial implications.
What is effluent and where can it be found on the railway?
Effluent is any liquid waste that arises from domestic or industrial purposes that is discharged from a particular source and released into the environment. It can be separated into three categories – domestic effluent, trade effluent and surface drainage. The most common form produced within the rail industry is trade effluent, which arises from industrial and commercial activities, such as train maintenance and cleaning activities.
Effluent is created at every railway maintenance depot, and while its quality and quantity may differ, wastewater and discharge is commonly generated by a number of methods:
- Leakages and seepages can occur from both stabled rolling stock and depot facilities such as refuelling systems. Contaminants such as diesel fuel and lubricant oil from engines can leach into the track ballast and potentially contaminate track drainage systems, while leakages from storage tanks, supply pipework and pumps can lead to contamination of nearby drainage systems
- Small quantities of diesel fuel/engine oil and coolant can be spilled during the routine servicing and maintenance of rolling stock. This can contaminate the surrounding area, usually in areas of the depot such as inspection pits and fuelling aprons. The waste from maintenance and servicing activities contributes to the majority of pollutants found in effluents at rail depots, including diesel fuel oil, engine lubricant oil, hydrostatic and gearbox oils and detergent-based cleaners
- Surface water arising from rainfall runoff originates in access roadways, car parks, areas of hardstanding and track drainage. Surface water drains are prone to contamination from accidental spillages, leakage and historical contamination
- Exterior cleaning of rolling stock, together with the cleaning of shed floors and depot inspection pits to remove the build-up of dirt, oil and grease can give rise to considerable quantities of effluent, with several cubic metres of aqueous effluent generated each day. Various detergents are used depending on the type of dirt requiring removal, and some of the cleaning chemicals can be hazardous to the environment if spilled or stored incorrectly, or if they are not used at the correct strength.
Are there any legal implications surrounding the management of effluent?
Managing environmental pollution and consenting discharges to controlled water is a legal requirement, as well as being part of an organisation’s corporate social responsibility. Businesses in England and Wales must comply with a range of legislation restricting the amount of effluent that is released into sewers or water courses, including the Water Resources Act (1991), Water Industries Act (1991) and Environment Act (1995). Companies in Scotland meanwhile, must comply with Section 26 of the Sewerage (Scotland) Act 2002 and Water Resources (Scotland) Act 2013.
Discharges of trade effluent to foul sewer systems are subject to consents issued by the local water utility company, while discharges to controlled waters such as streams and rivers are subject to permits issued by the applicable environmental agency. Any organisations found responsible for causing pollution or discharging effluent without the consent of the applicable environmental agency or their local water utility company face substantial fines and prosecution, causing negative publicity for the business.
Consent limits restrict the daily volume and maximum discharge rates for effluents, while also setting quality thresholds for a range of chemical parameters. Any effluent released from depots must meet these quality standards, and failure to comply with specified limits – such as pH, suspended solids, oil content and Chemical Oxygen Demand – is considered a legal offence. It is therefore vital that rail organisations have all of the correct consent documents in place for all of their sites to ensure legal compliance.
How can effluent be effectively managed so as not to cause environmental harm?
Rail organisations must identify the on-site activities that take place at their depot that could contaminate drainage systems with effluent, while also understanding the full extent of the environmental risks posed by these activities. Having the appropriate management procedures in place can help to prevent contaminants from entering drains, as well as reassuring organisations that they are adhering to the appropriate legal constraints and minimising environmental harm.
Preventing oil and other contaminants from entering susceptible drainage systems is the first stage of risk management. Site risk assessments can be carried out to identify activities that can affect effluent quality and identify potential Source – Pathway – Receptor scenarios. Different drainage systems on site should be mapped and their layout understood, with gully drains, collection sumps, inspection chambers and manholes clearly identified and correctly colour coded to reflect their status. Collection trays and absorbent materials are commonly used within the rail sector, catching spillages at the source and minimising the risk of contaminants entering drainage systems.
Prior to discharge off site, the majority of effluent discharges from railway sites require some form of treatment. These can range from simple settlement chambers to remove solid material to complex multi-chambered interceptor systems to remove free oil. In some cases, additional chemical/physical treatment may be required depending on the nature of the contaminants present.
Monitoring programmes should be implemented to ensure that effluent discharges to the foul sewer meet the required terms of consent to discharge, or in the case of unconsented discharges to controlled waters such as clean run-off water, that no unexpected contamination is present. The findings of such monitoring programmes in addition to highlighting non-compliance also allows for remedial action to be taken before a major incident can occur.
It is also essential that all staff carrying out activities where effluent is generated are adequately trained to respond to all possible effluent scenarios on site, making sure they are aware of the consent guidelines in order to remain fully compliant. SOCOTEC provides a host of environmental monitoring services to ensure that your business maintains full legal compliance when it comes to trade effluent or surface water discharges.
Legionella Roles and Responsibilities
From depots and on-board facilities to redundant outbuildings and old carriage wash systems, Legionella bacteria can grow in a wide range of locations within the rail industry. But who is responsible for managing the risk of Legionella and ensuring the health of safety of employees and the general public? In this blog, Paul Sear, national technical manager within SOCOTEC’s Water Hygiene team, explores the role that rail organisations must play with regards to Legionella management and the various responsibilities that this entails.
Which areas of legislation must rail organisations comply with in terms of Legionella management?
The only area of legislation which provides specific advice and guidance for Legionella management and control in standard water systems is Legionnaires’ disease: The control of Legionella bacteria in water systems, Approved Code of Practice and Guidance on Regulations (L8). Written and published by the HSE, ACOP L8 is a legally binding document aimed at those in control of the premises (otherwise known as duty holders), providing advice and guidance on how to identify, assess, manage and control the risk of Legionella in the workplace. In addition, HSG 274 provides technical guidance on the management of Legionella risk in different types of water systems. Part 2: The control of legionella bacteria in hot and cold water systems bears the most relevance for the rail industry with regards to on board water systems, outlining the monitoring and maintenance regimes and their frequencies required to ensure health and safety.
In terms of more general legislation that covers Legionella management, the Health & Safety at Work Act 1974 states that the duty holder has a duty of care to ensure the health, safety and welfare of employees so far as is reasonably practicable. What’s more, Legionella is considered hazardous to health under the Control of Substance Hazardous to Health Regulations 2002, which requires duty holders to undertake a risk assessment and, if there is a foreseeable risk, implement suitable control measures and ensure that the individuals responsible for managing this risk are suitably and sufficiently trained.
Similarly, need to manage the risks posed by Legionella also falls under the Management of Health & Safety at Work Regulations 1999, which highlights the importance of processes and procedures to prevent the growth of Legionella bacteria, as well as discussing the appointment of responsible persons to implement adequate control measures. Within this specification, responsible persons must undertake risk assessments, training and implement procedures should serious issues arise, such as an employee contracting Legionnaires’ disease.
Other legal requirements for Legionella management include the Notification and Cooling Towers and Evaporative Condenser Regulation 1992 and the Reporting of Injuries Diseases and Dangerous Occurrence Regulations (RIDDOR) 2013. There are also many British Standards providing advice and guidance on how to manage the risk, including BS 8580 Water Quality – Risk Assessments for Legionella Control – Code of Practice and BS 7592 Sampling for Legionella Bacteria in Water Systems – Code of Practice.
Who is considered a responsible person when it comes to Legionella management?
The role of a competent/responsible person is set out in paragraphs 48-57 of ACOP L8, and this individual must be specifically appointed in writing by the duty holder or their representative. In order to qualify for the role of responsible person, the individual in question must have sufficient authority, competence and knowledge of Legionella and the systems they are responsible for, and will more than likely be working within a management-based role in the facilities, estate or health and safety sectors.
The appointed responsible person will manage the level of risk on a day-to-day basis, and it is their duty to ensure compliance by undertaking Legionella risk assessments, implementing a written scheme of control and ensuring that records are kept and that anyone involved in the Legionella management process is suitably trained and competent. Inadequate management and lack of training are contributory factors in most cases and outbreaks of Legionnaires’ disease, and it is vitally important that the competent person is fully aware of their responsibilities and has up-to-date knowledge and awareness of Legionella to ensure that they are fully capable of effectively managing the level of risk.
Legionella growth within the rail sector
One of the main legal requirements within ACOP L8 is for duty holders to have an up-to-date, suitable and sufficient Legionella risk assessment for their water system in place. This requires responsible persons to identify any potential hazards, consider who may be at risk of exposure, keep records and implement/review control measures. Furthermore, having the appropriate control measures in place will allow rail operators to control the conditions in which bacteria can multiply, reduce aerosol generation and human exposure. There are a variety of precautions that can be implemented to minimise the risk of bacterial growth, including temperature control, regular turnover of fresh water, cleaning and chlorination, sampling and water pre-treatment.
Another legal requirement under ACOP L8 is to ensure that water systems are regularly monitored and maintained in line with the recommendations outlined within your Legionella risk assessment and written scheme. Based on the control measures you already have in place or the recommendations within your risk assessment, a monitoring programme is necessary in order to demonstrate that these control measures are effective. Examples of control measures include regular flushing, temperature monitoring, chemical level checks, condition inspections, cleaning, disinfection and sampling. How often you will need to carry out monitoring is referenced in the Technical Guidance document HSG274 Part 2 provides guidance on monitoring tasks and required frequencies.
Finally, keeping records of all aspects of your organisation’s Legionella control and management process is essential in order to demonstrate that your water systems are under control and well managed. Information that should be recorded includes names, positions and contact details of those involved in the control process, a copy of the risk assessment, method statements and a log for contractors, consultants and visitors. By keeping this evidence up-to-date, you will be able to demonstrate to the Office of Rail and Road (ORR) and the HSE that you are effectively managing the risks present within your water system.
The impact of COVID-19
It is a well-known fact that Legionella bacteria thrives in stagnant conditions, and given the increase in the number of employees working from home since the beginning of the pandemic, it is vitally important that water services in depots, stations, offices and on-board trains are being flushed on a regular basis to replicate normal usage as much as possible.
As we begin to slowly ease out of the third national lockdown and return premises back to their normal level of occupancy, it is important that water systems remain safe for people to use. If systems have been out of use, they must be recommissioned correctly.
Emily Hill is communications executive at Socotec.
For more information visit www.socotec.co.uk