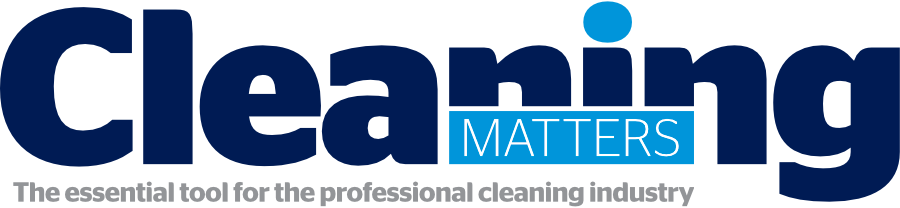
![]() |
Chris Shaw
Editor |
Home> | FACILITIES MANAGEMENT | >Window Cleaning | >Scaling the heights of safety |
Scaling the heights of safety
11 October 2022
Ian Sinclair discusses the importance of safety while working at height and Principle Cleaning Services’ approach.

THE HAZARDS around any working at height are well documented but the sad fact remains that this is still the main cause of fatalities in the workplace.
According to HSE Workplace Fatal Injuries in Great Britain, 2022 - the main kind of fatal accidents for workers (2021/22) were caused by a fall from height, with a total of 29 fatalities, accounting for 24 per cent of all worker deaths over the year.
The WAH Regulations 2005 (amended 2007) have brought about a huge shift in changing attitudes and behaviours to this issue with innovative and cost-effective alternatives to traditional access methods but after c.16 years of being in operation, is there the possibility that we have become a bit blasé and complacent?
Do we all just presume that everyone is adhering to the hierarchy and that all workers at height are aware of the risks involved in these practices and the consequences if they don’t? Regrettably, this isn't the case, which is clearly borne out by the continuing grim statistics of fatal injuries.
Equipment and procedures
It goes without saying that he quality of equipment is paramount with maintenance regimes governed by the Lifting Operations and Lifting Equipment Regulations 1998, and the Provision and Use of Work Equipment Regulations (PUWER) 1998.
Systems and procedures can be implemented, equipment checked and monitored but it only takes a split-second lapse in concentration for a serious adverse event to occur that can result in devastating consequences for so many.
This potential issue was identified and discussed in great depth by the senior management team at Principle and it was recognised that, regardless of experience, the risk remains, with the real possibility for operatives to allow unconscious competency to become the norm.
It is generally accepted that those operatives who work at height on a full-time basis are fully conversant with the risks involved but at a recent behavioural safety training session, it was highlighted that it is possible to carry out daily checks of harnesses and other equipment without actually realising it is being done, i.e., on autopilot or with unconscious competency. In other words, carrying out the required pre-use checks as a matter of course because that is what is required but potentially, without actual substance or meaning.
So, what do we actually mean by unconscious competency? There are four stages of conscious competence:
- Unconsciously incompetent - an inexperienced operator who is unaware of the risks involved in the task they are completing
- Consciously incompetent - an operator with limited experience but who is beginning to understand and recognise the risks involved
- Consciously competent - an experienced operator who is fully aware of the risks involved and is focused at all times
- Unconsciously competent - an experienced operator who is simply ‘going through the motions’ without realising that their level of awareness is potentially falling into incompetence.
Keeping operatives safe
Within Principle, in an effort to ensure that operatives remain safe, focused and aware at all times, an extensive, refresher safety training programme was embarked on at the beginning of 2021.
But even before this initiative commenced, a rolling programme of three-yearly, safety-critical health assessments was implemented for all operatives who work at height. These are carried out by the organisation’s approved occupational health assessor and this gives both the company and operatives confidence that they are fully fit to work and withstand the rigours of extreme temperatures and associated physical bodily stress.
This initiative was welcomed and embraced by the workforce as a positive step in terms of understanding their own health status and, how they could improve their lifestyle by healthier eating, exercising and monitoring their use of alcohol and nicotine. Team members need to be fit and well for the task in hand for everyone’s benefit.
Training and development
The senior management team also attended a Working at Height Safety Behavioural training day, which was pivotal in raising awareness to the concept of the levels of competency and, more importantly, incompetency - by unconsciously going through the motions without actually comprehending what they were doing and why they were behaving in a particular way.
This training is now being cascaded down to supervisors so that they can begin to recognise where possible acts of unconscious competency might be taking place, unbeknown to the operative concerned.
It is not just limited to the operational workforce, working at height activities can be viewed as complex and difficult to understand with numerous unfamiliar terms and phrases. Where our site managers are responsible for both horizontal and vertical activities, should a challenge or concern arise, managers can contact the relevant in-house expert to assist and advise on the best course of action but, where given the relevant training, they are in a much better position to resolve the issue themselves.
A bespoke, in-house, Managers Working at Height Awareness training module is being developed, which will give a basic understanding of legal requirements, terminology and definitions that will develop and support a manager’s knowledge and experience of working at height activities.
We are not expecting them to become experts overnight but seeking to take away the fear factor and give them the operational knowledge and information to raise their confidence in dealing with this complex subject.
Additional resources
To further support these initiatives, a custom-made internal audit process has been developed and is being introduced across the business. These audits are carried out by the health and safety department who are independent of operations and give a fully objective account of the processes and systems being administered.
They are not just limited to ensuring that risk assessments are in place and being briefed to the workforce but that all inspections are completed and meaningful along with checking that all other company and legal requirements are being carried out. Observational and interview audits are also included in the overall process in order to get a holistic perspective of the safety culture at a site.
Principle’s Vertical Safety and Compliance Manager is well known and has developed positive working relationships within the business, having extensive operational experience of working at height activities including rope access and cradles and being fully conversant with the challenges faced every time an operative puts on a harness or checks a karabiner.
Operatives are observed while using equipment to ensure that all procedures are being adhered to and this is supported by carrying out both pre and post operational interviews with the teams so that their actual understanding of their own safety behaviours can be determined.
Managers and operatives could become defensive and feel that they are being criticised and the audit process can then potentially become a negative and demoralising exercise for those under the spotlight, so Principle is adopting this different approach.
Yes, some elements that require improvement or rectification might be identified but, more importantly, they highlight good working practices and operatives’ commitment to building a robust safety culture.
From these positives, best practice can be shared across the business to further enhance its overall safety performance and, where any shortfalls are identified, these are fully explained to the team with a plan and timescale for rectification.
Conclusion
As with any management system, be it safety, quality or other, a programme of continuous improvement needs to be adopted to ensure that the systems and processes remain relevant to the needs of the business but also to the needs of those who are required to operate ‘on the front line’. Merely carrying out a process because ‘’I have been told to do it’ is not enough - operatives need to understand why they are being instructed to undertake a particular work instruction.
Principle’s vertical operations have grown organically over time, laying the foundation of a solid safety culture but, as the business continues to expand, the internal communication of relevant safety policies and procedures and, vitally, cultural understanding, must go hand-in-hand in order to ensure and demonstrate not just compliance but also of what is required and expected of employees by the organisation and its current and future clients.
Ian Sinclair, CMIOSH, Dip. RSA is head of safety & compliance at Principle Cleaning Services
For more information visit www.principleclean.com
- Industrial rope access: A window of opportunity
- First cleaning contractor in Europe to achieve CIMS accreditation
- Next generation cleaning
- Principle retains Broadgate portfolio
- Principle contract wins
- Partnership set to 'revolutionise' window cleaning across London
- Reducing its impact
- Principle celebrates frontline cleaners
- Utilising robotics in contract cleaning
- Principle Wins Crick Award for Supporting World Class Science