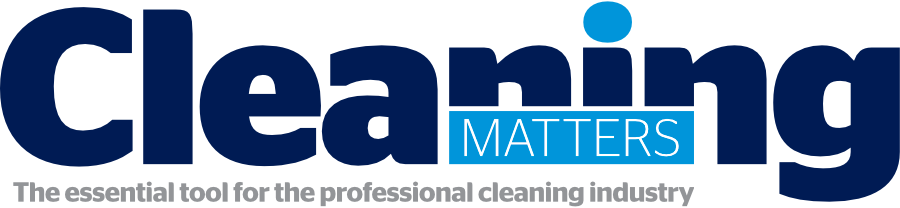
![]() |
Chris Shaw
Editor |
Home> | FACILITIES MANAGEMENT | >Health, Safety & Workwear | >It's time to set cleaner air targets |
Home> | FACILITIES MANAGEMENT | >Infection Control & Prevention | >It's time to set cleaner air targets |
Home> | FACILITIES MANAGEMENT | >Waste Management | >It's time to set cleaner air targets |
It's time to set cleaner air targets
28 March 2022
Rebecca Munson examines why achieving higher air quality inside and outside should be a priority for businesses. So how can this be efficiently achieved?

I BELIEVE it has been all too easy for organisations and individuals to think that improving air quality is someone else’s responsibility. However, that isn’t the case, more than ever right now as air quality has been linked to climate change. We all have to do our part, globally, to make improvements, especially in industry.
Companies add to a collection of problems that affect the entire planet – every emission piles up, and joins a chain reaction of destruction affecting environment and people in the most detrimental ways to their health. We must understand the negative effects we are experiencing now, and how we can create opportunities by our actions to effect change.
What’s broken?
At the Clean Air Summit in February 2022, Professor Chris Whitty, England’s Chief Medical Officer, was noted to have said that air pollution is everybody’s problem, but solvable. He also indicated that in the UK, we haven’t been paying as much attention to it as we should have. Giving the medical practitioner’s view, he highlighted the serious health problems that can be caused by poor air quality – cardiac, respiratory and cancerous – and the connections can no longer be ignored.
Based on the Health & Safety Executive’s (HSE) most recent statistics published in 2021, work-related lung disease is estimated to claim 12,000 lives annually. On top of that, there are approximately 17,000 new cases reported each year that are caused or made worse by work, in addition to the new or long-standing cases 47,000 from the previous year.
The WHO (World Health Organization) undertook a study recently that confirms that the situation is worse than we think. WHO figures show that air pollution is causing seven million deaths annually worldwide, because 2.6 billion people rely on polluting technologies for fuel and cooking. Furthermore, 91% of the world’s people live at risk in places where air pollution rates exceed WHO safety guidelines.
Employees care about good air quality at work
Air pollution awareness has more of a profile in high risk workplaces. Let’s look at construction as an example; construction or demolition dust is hazardous if not managed in the work setting can cause short and long term damage to unprotected employees with respirable dust and inhalable dust. Between them they are responsible for respiratory diseases like asthma, chest infections, COPD (chronic obstructive pulmonary disease).
The quality of the internal working environment however, has become a key criterion for existing and prospective employees when it comes to staying power.
In an occupational air quality study carried out in 2019 by Remark Group in the UK, there were some startling results. Nearly 90% of respondents reported that they felt sleepy during their working hours. 80% believed that poor air quality impacted their productivity and their health and wellbeing.
We’ve all had that surreptitious nod at our desk in a stuffy, hot office in the afternoon. It creeps up on you, as your oxygen quality diminishes, making you sleepy and your thinking fuzzy. Those occurrences are not helpful to nurture productive or happy employees. It’s also a breeding ground for error as mental acuity is affected.
Outside airborne pollutants find their way to us in our internal environments as long as there is a conduit. HVAC systems intake will capture some pollutants, even if they are filtered as if not maintained properly, filters degrade. Or there’s pollution risk by just opening windows and doors. Therefore, monitoring air quality inside seems like an obvious measure to ensure that employees are not subject to inferior air quality that compromises their wellbeing. Efficient air filtration to maintain adequate levels is also the next logical step because there should be no compromises on the quality of air that we breathe.
We also can’t ignore that the pandemic has brought the internal air quality into sharp focus, as we fight against the airborne coronavirus. Moreso as employees have been asked to return to the office, working and breathing alongside their colleagues, with some trepidation in many cases.
Decarbonise – to reduce the transferable risk
We are seeing the more devasting effects of poor air quality on the public – not just in industrial situations, but their effects spill over into the public realm. There is an inextricable relationship between industrial activity and the negative effects on the general population.
Over the last two years, 17,000 people were admitted to hospital for asthma as a direct consequence of poor air quality, as an example.
This is where decarbonising supply chains makes a positive impact. Crucially, it tackles an environmental threat from a cultural level, encouraging the pledge to use a cleaner solution wherever possible and make it the new norm. If the technology exists, and is cost effective, why not use it?
We know that the government has brought in targets, such as the phasing out of diesel / hybrid vehicles by 2035, and the introduction of clean air zones. There are also initiatives like Co2nstructZero in response to the UK Prime Minister’s ten point plan to reach Net Zero by 2050.
In the UK, dangers to construction workers were highlighted by the British Safety Council (BSC) in 2019. It petitioned for air pollution to be classified as an occupational health hazard in construction, calling for a workplace limit to be placed on diesel fume emissions. The BSC even took its request to COP26 summit in November 2021 to garner support for outdoor workers as part of their Time to Breathe campaign.
The current reforms on the use of Red Diesel and other rebated fuels will also compel a rethink on what fuels certain industries use in their equipment, even what equipment they use.
My organisation is particularly interested in this pollution risk, and as a result we are developing zero emissions safety solutions for high risk industries - the first being the UK’s first battery operated dust suppression system for use in construction, waste and recycling and other dust generating industries. It’s battery operated so no there’s no diesel use; it’s quiet so there’s no noise pollution either, and runs for a whole day on a charge.
However, on the ground, responsibility really needs to be taken by companies themselves. Championing sustainability and being sustainably active are two different things. Therefore being committed to policies that are enacted on a daily basis in a company’s dealings will be so effective for a cultural and behavioural change.
Solutions need not be complicated. Re-using familiar technology in different ways can spark a cultural change in our supply chains if we don’t shy away from it. Concerns along the supply chain about using ‘new’ technologies like this are often cost based. However, to decarbonise the supply chain would likely transfer a small percentage more cost to the end user, to make a significant and positive impact. Look at the the rising prices of diesel in our growing energy crisis? Surely it makes financial sense to find a more cost effective solution to replace it, transfer less cost to valued customers and also meet the UK’s Net Zero goals?
The hardest part of the process is making the decision to use green solutions going forward. The adjustment follows.
Make clean air a priority in industry
There is so much that can be prevented by establishing a plan that identifies all risks to employees clearly. From this identification, a targeted health and safety plan can be created for each site.
Health & Safety managers must be diligent with producing method statements, risk assessments, and relevant data sheets. By conducting this kind of due diligence, gaps in air quality improvements can be identified and addressed. It’s doubly important that employees are encouraged to read and heed them to protect their health on the job.
It's also important for employees to feel that they can question any safety guidance. Especially if they are working in the hazardous conditions every day, or handling hazardous materials. So, if safety guidance provided isn't compatible with what risks actually occur on site, then changes may need to be made.
And last but not least always wear PPE and use safety equipment, like dust suppression, or air monitoring and purification systems that tell you when your immediate air quality needs addressing. Then act.
Going forward
At Air Spectrum, we seek to create the greenest solutions to improve air quality because we realise that the clock is ticking and the situation is getting worse. To achieve Net Zero successfully by 2050, decarbonising of supply chains is vital as we build a more sustainable future. The most important stage of change is commitment to make a difference, and follow through. The solutions are there, we just have to embrace them, abandon any fear of doing things differently and be open to possibilities.
Rebecca Munson is managing director of Air Spectrum Environmental.
For more information visit http://www.airspectrum.com