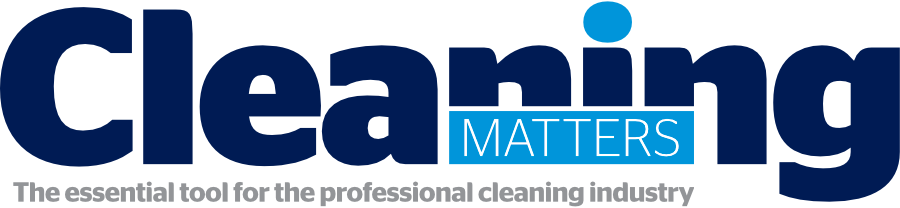
![]() |
Chris Shaw
Editor |
Home> | FACILITIES MANAGEMENT | >Health, Safety & Workwear | >Keep it clean: The dangers of not meeting health and safety regulations |
Home> | INDUSTRIAL CLEANING | >Industrial Equipment & Services | >Keep it clean: The dangers of not meeting health and safety regulations |
Keep it clean: The dangers of not meeting health and safety regulations
13 January 2020
Anh-Tai Vuong, president, DuroVac, discusses industrial cleanliness, some of the key risks to consider and the necessary solutions to prevent them.
Keeping employees safe and healthy requires knowledge of industrial hygiene, which involves recognising, evaluating and controlling environmental stressors in the workplace. Businesses without an organised or dedicated approach to industrial cleanliness will be at greater risk of injuries and illnesses and see increased rates in employee turnover.
The hazards
There are many potential hazards that can be caused by improper industrial hygiene.
Machine pollution or tools inside buildings, highway pollution and dusts from mechanical processes, reduce indoor air quality, which can lead to health concerns from chronic coughs to nausea to severe headaches.
Chemical hazards take many forms, from liquid to fumes to dusts, and can be absorbed, inhaled, or ingested into a worker’s system. Exposure to chemicals commonly used in workplaces can lead to a variety of short- and long-term health effects such as poisoning, skin rashes and disorders of the lung, kidney and liver.
Ionising radiation can be found in settings ranging from healthcare facilities to nuclear reactors and their support facilities. This type of radiation damages cells and possible long-term effects include cancer and sterility.
Biological hazards exist in most workplaces that involve working around other people, unsanitary conditions, in labs or in the environment. Some examples of biological hazards include; mold, sewage, blood and airborne pathogens.
These sources can cause a variety of health effects ranging from skin irritation and allergies to infections such as tuberculosis and Lyme Disease.
Assess the risks
Strong industrial hygiene policies are necessary to reduce these hazards as much as possible and begin with good risk analysis. One of the most effective methods is to break jobs into a manageable number of tasks, work with and observe employees conducting these tasks, and pay close attention to the actual and potential hazards.
Be sure to split these by their relevant groups (eg: chemical, biological and physical hazards) to make it easier to plan the exact safety requirements needed.
Remember to plan for short-term exposures too, especially when they're not conducted daily. For example, there may be a cleaning solvent that is occasionally used and while the entire duration of exposure may be low, high concentrations could still pose health risks.
Once hazards are identified, introduce controls to limit exposures or reduce the consequences of exposure. Remember to use the hierarchy of controls as a guide to remind the team eliminating the hazards is always the best option. You should resort to personal protective equipment after more effective controls have not reduced exposures to acceptable levels.
You need to ensure the level of detail in a risk assessment remains proportionate to the risk. This can be tricky to do, as industries such as the pharmaceuticals sector continuously advance. New substances need to be added to assessments and examined to determine risk control.
Finally, when monitoring a workplace environment make sure you also know which analytical method to use in advance of sampling hazards such as respirable silica, to avoid delays in completing chain-of-custodies. There are specific OSHA requirements that should be adhered to.
For instance, the recent silica rule states employers must provide staff with the results of monitoring, and information about any corrective actions taken within five working days in construction, or 15 working days in general industry and maritime.
Putting practices in place
Many workplaces are still in need of better industrial hygiene products to eliminate risks such as professionally designed industrial fume extractors or proper industrial dust collection systems.
Ordinary ventilation systems that are not part of purpose-designed industrial dust collection systems will almost certainly concentrate dust in hard-to-access ducts and other damaging places. In time, hidden dust accumulations pose serious risks of fire, explosion or toxic air quality.
Consider large central vacuum systems and powerful portable vacuums instead, which are designed to remove harmful particles or hazardous messes from any size warehouse. These systems are the best way of controlling dust, as they cut cost and time spent removing waste, removing up to thousands of pounds (lbs) of dust per hour.
Built-in HEPA filters also trap 99.9 percent of dust in the vacuum, so it’s not released back into the air, reducing the risk of dangerous airborne particles. Use mats, platforms, false floors or “other dry standing places” where useful, to prevent any accidents from spillages in workplace areas.
When possible, safety warning signs should be used, when certain tasks occur (eg: if floors are slippery). Cleaning chemicals, products and potentially dangerous equipment should only be used by appropriately trained individuals or under supervision.
Those responsible during the cleaning process should be careful not to block fire exits or staircases with equipment or waste and should check they are not leaving trailing electrical cords on floors.
The training zones
When it comes to training employees, knowledge is never enough. It’s a necessary pre-requisite in many situations, but there’s always room for more. And that comes in the form of application. Demonstrations, practise, and feedback from an experienced teacher are essential to get the best results.
Scenario-based learning is a highly effective training method, to see which hazards employees are correctly identifying and which they’re not. Post-training quizzes, employee surveys, and official certification exams are some of the best ways to measure training effectiveness.
The more data you collect on measurable outcomes, the easier it will be to quantify your company’s return on investment.
Make it easy for all workers – both health and safety professionals and other staff – to adhere to health and safety processes by labelling all materials and including information about strength, ingredients and steps to take in case of misuse.
Make logbooks containing all details on how to handle, transport and store all materials available in every warehouse, factory or facility, so employees can ensure best practice and not slip back into old habits once training has been completed.
About Anh-Tai Vuong
Anh-Tai Vuong is president, corporate sales and business development, at DuroVac, a manufacturer of industrial vacuums designed for rugged applications. With a Bachelor of Engineering from McGill University, Vuong has worked in industrial sales his entire professional life. He specialises in aluminium smelters (primary metals), potash and fertilizers (mining), steel mills and foundries (primary metals) and combustible dust.
- Agenda announced for Cleaning Excellence Conference & Awards
- Harrisons announces acquisition of Ecotech (Europe)
- COVID-19: ExCel to be turned into emergency Coronavirus hospital
- Hand sanitisers market witnesses global growth
- Fire damages Green Machines factory in Falkirk, Scotland
- Spring clean: Turning clutter into cash
- Businesses must stick to hygiene laws warn FTA, RHA and Unite
- Guide provides advice on communications with furloughed FM employees
- British Cleaning Council asks to meet minister to discuss key industry issues
- Global industrial floor scrubber market to surpass $2.9billion in 2020