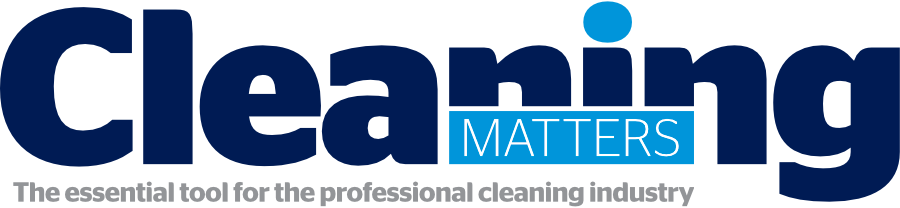
![]() |
Chris Shaw
Editor |
The new industrial revolution
07 November 2016
A dramatic change in how we clean is being powered by users as well as equipment manufacturers across multiple countries, explains Dianna Steinbach, director EMEA Services at ISSA
Our market is folding into the next industrial revolution or, as some call it, Industry 4.0. and I believe the ensuing technology has the potential to reshape the commercial and institutional cleaning industry’s future success.
It could be seen in the fact that the Innovation Lab at this year’s ISSA/INTERCLEAN Amsterdam show drew record visitor numbers to view the latest tech developments. Similarly, the neighbouring Management & Mobility Solutions Pavilion was among the very busiest areas of the exhibition with attendees checking out the latest apps, on-line monitoring tools, e-learning platforms and workflow management software. The Industry 4.0 topic also came up in educational conferences and networking events in which ISSA participated in Australia, Germany, Italy and Spain in October alone.
The Industry 4.0 concept
The key promise of the Industry 4.0 concept is as striking as it is fascinating: we are about to witness a new industrial revolution, fuelled by the advancement of digital technologies. The fusion of the physical and the virtual world into cyberphysical systems will have a disruptive impact on every business domain. Of course, there is a real possibility that the hype surrounding this latest development could well outpace the reality for many sectors. There is much that still must be done with good old elbow grease and human observation in our industry for sure. Yet, I believe that there will be opportunity for the commercial and institutional cleaning industry.
First, you must understand the crux of this latest industrial revelation. It is no longer about how we make things, it is about how they communicate with one another and share information. The benefits to our industry are boiled down to three main areas: the ability for cleaning operations to better understand themselves through the data their machines provide, for cleaning operations to utilise the data provided by smart buildings in which they operate, and the ability for cleaning operations to use both to help facility decision makers better understand needs and better meet them through more targeted services.
You likely have begun to see developments on at least the first two fronts. Multiple machines are providing usage data and location tracking. I recently heard an equipment manufacturing CEO explain how their data helped a customer determine that they were vastly overestimating the use time of their machines. This can lead to work-loading efficiencies by better understanding over how many hours that specific work is conducted. Instead of rushing workers to improve productivity, managers can better deploy those workers with more accurate usage data.
Downtimes and delays also can be reduced if preventative maintenance can be conducted based on machine alerts. Not to mention the value of tracking to find out that subcontractors have walked off with machines you thought were in use.
Turning to smart buildings, we are just starting to see our industry take advantage of the data available, such as occupancy sensor information that helps determine which areas of a facility were even used and warrant cleaning on a given day. Hospitality and healthcare facilities in the UK and many other countries are using integrated systems to alert cleaning staff when rooms are ready for turnover. Tracking software also can help managers ensure that remote staff are where they should be when they should be, and remain safe.
'Reversing our current dilemma'
When we begin to understand and harness this increasing amount of information, I believe the cleaning industry will be able to reverse our current dilemma where a large percentage of customers are ill-informed, requiring the wrong services, and pushing us to provide more for less in a dangerous race to zero. We have the opportunity to shed light on what really is needed to protect occupant health, conserve utility use and become a more valuable partner for facility stakeholders.
That said, it will take a corporate transformation to best leverage what the new industrial revolution offers. First, an organisation needs to determine which technology it wants to tackle first, whether within its own operations or within the facilities it serves. Then it needs to fully utilise the data available, or it will leave money on the table. Then there is the people investment: One service executive I spoke with said that what used to require the work of a part-time intern to manage the tech needs of a cleaning business, now could take four or more full-time and specialised staff. This is just at the corporate office alone.
New training also will be required for operations management and supervisors to understand how to digest and harness the data now at their disposal onsite. And our sales teams will need to acquire the knowledge to communicate new information to the facility decision makers within the context of a new value proposition.
The ISSA is setting up an Innovators Group in the UK to build engagement and ensure members can provide input that moves the industry forward. If you’re interested in participating, contact me at [email protected].
- ISSA/ INTERCLEAN CEE to share knowledge & best practices
- ISSA joins janitorial products export group
- Innovation for a new age
- ISSA appoints new European Manager
- Why sustainability is not just a drop in the ocean
- Eight simple steps to grow your business in 2013
- Do more than walk the aisles
- New beginnings
- Cleaning professionals must earn respect
- ISSA appoints business development manager for UK & Ireland
- No related articles listed