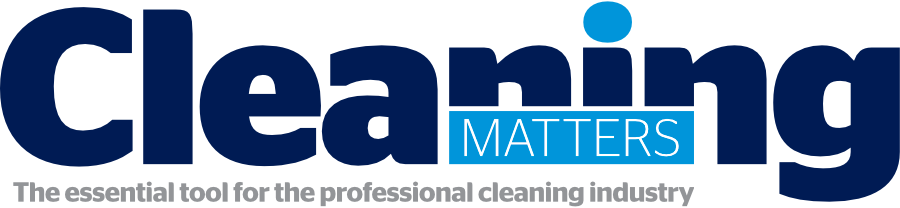
![]() |
Chris Shaw
Editor |
Home> | INDUSTRIAL CLEANING | >Industrial Equipment & Services | >The next ice age |
The next ice age
31 May 2016
Dry ice cleaning – also known as dry ice blasting – was developed in the 1980s as a non-erosive, water and abrasive media free way of cleaning heavy-duty production plant equipment. Stuart Wilders, market sector manager - advanced manufacturing, at BOC looks at how the process is evolving
Dry ice cleaning is well established in a number of industries where it is used in a wide variety of cleaning applications e.g. in moulds for foundries, tyre curing, vehicle seats etc. A major benefit of dry ice blasting is that this process can be carried out without having to disassemble any equipment.
Dry ice is made by compressing dry ice snow crystals to form 3mm diameter pellets which are then propelled by compressed air onto the surfaces to be cleaned. On impact, the solid pellet sublimes into gas which in turn transfers kinetic energy to the surface, causing contaminant embrittlement and detachment whilst minimising abrasion.
Compared to water, solvent or traditional solid blast media based cleaning processes, dry ice blasting offers many benefits; as well as being waterless and non-corrosive, it can clean hot surfaces and areas difficult for brushes to reach, with no hazardous chemicals and no residues. In most cases, cleaning with dry ice is far less labour intensive – and therefore cheaper than other cleaning methods.
Let it snow
In recent years, carbon dioxide cleaning processes have evolved to handle the cleaning of high quality components which could be damaged by more abrasive processes. Snow cleaning, created by de-pressurising liquid carbon dioxide to form tiny dry ice crystals (approximately 10 microns), is most effective for the cleaning of mould release agent residues, oil films, dust, fingerprints and smoke residue.
Snow cleaning is suitable for:
- cleaning prior to painting, lacquering, coating or gluing of plastic components cleaning of production tools (e.g. moulds)
- spot cleaning of electronic boards
- removal of flash from machined parts
- cleaning during machining processes
- anti-corrosive oil removal prior to joining of parts
- removal of small contaminants from drilled and tapped holes.
Automation & robotics
In the plastics processing industry, traditionally manufacturers used large-scale aqueous cleaning plants to clean plastic parts including bumpers, outer mirrors, grills and headlights. Nowadays, plastics manufacturers are investing in more modern, automated snow cleaning systems combined with robotics. Cleaning processes lasting several minutes followed by long drying processes have been replaced by snow cleaning systems which not only significantly cut the overall cleaning time but also reduce requirement for capital investment, power costs and plant footprint.
This group of technologies continue to develop. A further innovation incorporating both snow and abrasives was launched in the UK earlier this year. An alternative to manual abrasive cleaning, this is a combination of snow and abrasive, the ratio of which can be adjusted dependent on the nature of the contaminant. The introduction of carbon dioxide into the abrasive cleaning process means less hazardous abrasive product is required, whilst the tiny carbon dioxide crystals ensure cleaning right down to the surface microstructure. Within metal additive manufacturing processes, the technique has been adopted to remove surface oxidisation as well as any un-fused metal powders.
In the UK, companies considering upgrading their cleaning processes can take advantage of the Automated Robotic snow cleaning demonstration facility at BOC’s Manufacturing Technology Centre in Wolverhampton. Manufacturers have the chance to test their own products in cleaning trials using the Cryoclean range of carbon dioxide snow and ice solutions which have been developed and refined by BOC over the past years.
With objectives of reducing production downtime and driving down costs, dry ice, snow and snow and abrasives cleaning technologies give manufacturers a range of tools and a clean and hassle-free way to achieve a high-quality finish.