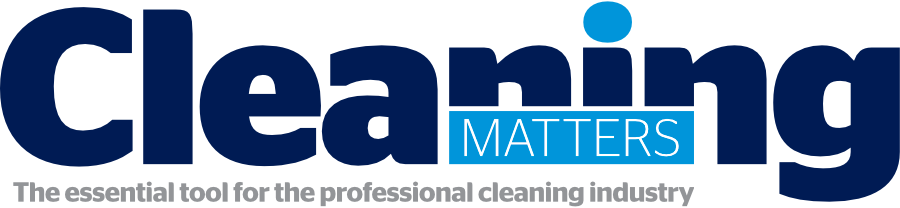
![]() |
Chris Shaw
Editor |
Home> | FACILITIES MANAGEMENT | >Health, Safety & Workwear | >Chemical labelling changes |
Chemical labelling changes
30 April 2015
The face of cleaning chemical labelling is about to change quite dramatically, chemical manufacturer RP Adam explains.

After years of debate the Classification, Labelling & Packaging (CLP) Regulations are about to come into force on the 1st June 2015. This means that any cleaning chemical manufactured on this date forward under law must be classified and labelled in accordance with the new CLP legislation.
There does seem to be a degree of misinterpretation from some companies who believe there is a two year grace period for this to come into effect – this is not accurate. To clarify, if product is made on the 31st May and sent from the manufacturer to a third party wholesales/distributor, that product can be sold with the old CHIP labelling for a period of two years. But let’s face it, how many distributors want to be holding two years stock – not one.
Most of the chemicals used in the professional cleaning arena are not intrinsically dangerous if used properly but as we all know some chemicals need more careful handling than others. CLP has been a laborious project for the chemical manufacturer but has put chemical health and safety right in the middle of the dance floor and if truth be known, it is probably one of the more sensible pieces of legislation to land on our door steps for some years.
From 'non-hazardous' to 'not classified'
CLP now completely eradicates the term "non-hazardous”, and companies need to be very careful when describing any professional cleaning detergent as such. The term to describe a product with no hazard pictogram is now "not classified”.
It is estimated that 80-90% of professional cleaning products currently available on the market will be classified as hazardous in some shape or form using the new CLP calculation method. RP Adam has taken a long hard look at our portfolio and considered carefully the options which were available to potentially to reduce hazard classifications. Initially we considered the perception of the professional user and perhaps rather neurotically thought that we might have had to make our well respected formulations weaker so that the ingredient concentrations would fall below the concentration thresholds set by the CLP Regulations.
But, then we concluded that this move would be short sighted and would reduce product performance – something we were not prepared to compromise on – our customers expect performance. We also had to throw into the equation that arguably, supplying less concentrated products would not be environmentally responsible because more volume would be used and more waste created.
User safety in the spotlight
We perceive this piece of legislation to be a pivotal moment in the professional cleaning arena, which puts chemical user safety at the top of the agenda. The good old days of "safe” and "dangerous” to use have gone, meaning that cleaning contractors and janitorial wholesalers, with the help of their chemical manufacturer(s) must provide their mutual end user customers with far more information than has been provided previously.
The industry needs to communicate the fact that these new hazard symbols should not cause alarm for the professional user, but in fact serve as a useful reminder of proper safety practices and the potential dangers if chemicals in general are not handled and stored properly.
CLP also assesses more ingredients to be classified as hazardous to the environment, so expect almost all concentrated disinfectant products to be classified as hazardous to the environment, including washroom and kitchen sanitisers and terminal disinfectants. However, as with all chemicals toxicity is only a matter of dose, and when diluted correctly the ready to use solutions will not be classified as hazardous.
Hazard descriptions in the text of SDS are all encompassing and err substantially on the side of caution. It should also be noted that they are relevant only to direct exposure to the pure substance. This can be an emotive area of confusion for the B2B customer. For example, concentrated acetic acid can sometimes be described as ‘fatal if ingested’ yet a 5% solution sold as vinegar is safe enough to use on food.
It is always important to treat all professional cleaning products with respect. Higher surfactant (cleaning) and biocidal active (germ killing) concentrations in respected professional formulations are required to get the job done in the real world.
Tea anyone?
So we provide an analogy here: You could think about (the new system) CLP and (the old system) CHIP in terms of sugary tea. Under the CHIP regulations, adding 10 lumps to your tea was assessed as dangerous, but adding 3 lumps might only need a health warning. However under the new CLP regulations 3 lumps is now considered dangerous to health and only 1 lump now needs a warning! The cup of tea is still the same as before, but the safe level for adding sugar is now lower - same tea, different rules!
RP Adam has been working on this classification project for well over a year and the administrative burden has been considerable but we are on plan to have all our formulations re-classified, new labels printed and product documentation updated. Downstream these changes to chemical hazard classifications cause several issues for the professional cleaning industry manufacturer, distributor and business consumer.
There will be a dramatic increase in the number of chemical products labelled with the "corrosive” pictogram. This is not because they have become "more dangerous” but as a result of a new system of classification. This pictogram can be used in three ways as 1) causes severe skin burns and eye damage 2) causing severe eye damage and 3) may be corrosive to metals. At first we believed this would deter B2B consumers but knowing that these very formulations were purchased in vast quantities for decades, why would the consumer start to turn their backs on the very formulations that had served them so well for so many years?
The PPE effect
The real issue here is for wholesalers and end users to now full accept that there will be a rapid increase for and provision of proper PPE (Personal Protective Equipment) for staff using professional cleaning products. From our experience across a wide spectrum of business channels we know that many reputable businesses today do not provide adequate quantities of PPE for staff; this now becomes a top priority.
Included in this this process RP Adam has decided that 95% of all our brands will have a front and back label. The front label will be an abbreviated version of our Product Guidance Sheet and the reverse will be a technical health & safety label. In essence all our new product labels will contain more product information, application advice and detailed health & safety information than ever before, so that the chemical container almost becomes a Product Guidance Sheet in itself.
After 1st June 2015, all hazardous products on the market will have new CLP warning symbols or pictograms (red diamonds) and warning messages on the label and safety data sheet. The chemical manufacturer has its work out here in terms of training and accurate communication, but as a basic list of key issues to be aware of we would recommend end users and wholesalers to:
- Look out for new labels and supporting product information and safety data sheets.
- Ask your chemical suppliers to train your employees how to recognise and understand the new label information.
- Ensure that sales teams are checking that the way end users apply chemical cleaning products are in accordance with advice from the supplier.
- Follow the advice provided on the new labels and in the updated safety data sheets.
- Check whether existing product hazard classifications have changed.
- Evaluate the risks to workers and update workplace COSHH risk assessments if necessary.