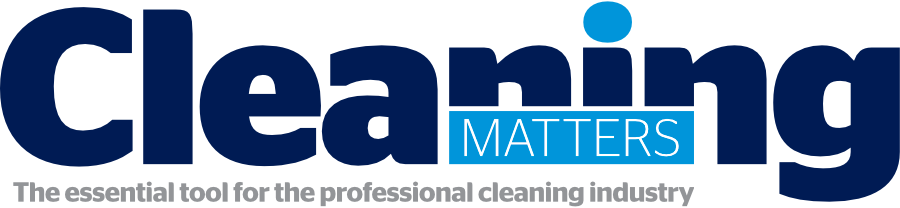
![]() |
Chris Shaw
Editor |
Home> | HOSPITAL HYGIENE | >Support Services | >Hidden hospital hygiene |
ARTICLE
Hidden hospital hygiene
07 March 2013
Hospitals naturally require the highest possible levels of hygiene - even in the hidden spaces where pipework and drainage systems are installed, says Peter Jennings, technical director for ACO Building Drainage
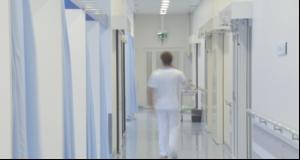
Hospitals naturally require the highest
possible levels of hygiene - even in the
hidden spaces where pipework and
drainage systems are installed, says Peter
Jennings, technical director for ACO
Building Drainage
In every healthcare environment the potential weak spot in effective hygiene control lies hidden underfoot in the pipework and drainage systems. Drains provide an ideal breeding ground for micro-organisms but the careful, informed specification and design of the drainage system can significantly minimise and control the risk of contamination.
A key weapon in the fight against bacteria is stainless steel, which is increasingly used to manufacture pipework that scores over cast or ductile iron in a number of ways. For example, internal cast iron pipe surfaces are prone to corrosion and fracture and can easily become furred and scaled, impeding the flow rate of drainage systems and leading to blockages that may force contaminated air or waste water to back up into hygiene-critical areas.
However, the strong resistance to corrosion offered by stainless steel represents a powerful defence against bacteria in hygienic environments across the hospital, from patient bathing areas to hidden pipework systems. In addition to offering a tough chromiumrich corrosion-resistant oxide film (CrO), stainless steel is also fireproof, resilient to rodent attack, and 100% recyclable.
Understanding the benefits By consulting the advice of an experienced manufacturer, it is possible to benefit from these and many other advantages offered by stainless steel and to avoid any complications that may arise, since even the best materials can pose problems if misunderstood or misused. For example, when cast iron or galvanised steel meet stainless steel, the contact results in galvanic corrosion in an aqueous environment. Even 316 grade stainless steel, which contains molybdenum and offers an even more resilient option than the more commonly used 304 grade, can be vulnerable to certain chemicals such as hydrochloric acid (HCl) and sulphuric acid (H2SO4). To ensure that all such issues are fully understood, ACO Building Drainage offers accredited CPD, available on a one-to-one basis or to large groups, giving advice on how to 'Specify It Right'. This kind of expert advice can be vital in helping all parties to make the right decisions when specifying drainage systems, particularly in hygiene-critical environments where all opportunities must be taken to protect patient health.
A corrosion resistance check-list, that takes into account factors such as the chemicals that will be present in the drainage system, typical concentration and temperatures, will help ensure that no crucial issue is overlooked during the specification process.
Fabrication processes naturally produce surface defects and imperfections of stainless steel so the correct post fabrication treatment is essential to restore the material to its optimum corrosion resistant state.
The ultimate finishing method is pickle passivation, a controlled corrosion process involving nitric and hydrofluoric acids that removes weld tint and iron embedded impurities introduced in the fabrication process and restores the chromium-rich oxide layer that naturally protects the material.
There are also options to consider regarding finishing, as this ultimately dictates the resistance of stainless steel to corrosion and bacteria; for example, electro-polishing flattens the surface of the stainless steel, which reduces the potential for bacterial growth.
Stainless steel pipework and drainage channels clearly offer the potential to provide healthcare institutions with long, reliable service to maximise budgets and safeguard patients. With the right specification and materials, the defence against bacteria in healthcare environments can be tougher than ever before.
In every healthcare environment the potential weak spot in effective hygiene control lies hidden underfoot in the pipework and drainage systems. Drains provide an ideal breeding ground for micro-organisms but the careful, informed specification and design of the drainage system can significantly minimise and control the risk of contamination.
A key weapon in the fight against bacteria is stainless steel, which is increasingly used to manufacture pipework that scores over cast or ductile iron in a number of ways. For example, internal cast iron pipe surfaces are prone to corrosion and fracture and can easily become furred and scaled, impeding the flow rate of drainage systems and leading to blockages that may force contaminated air or waste water to back up into hygiene-critical areas.
However, the strong resistance to corrosion offered by stainless steel represents a powerful defence against bacteria in hygienic environments across the hospital, from patient bathing areas to hidden pipework systems. In addition to offering a tough chromiumrich corrosion-resistant oxide film (CrO), stainless steel is also fireproof, resilient to rodent attack, and 100% recyclable.
Understanding the benefits By consulting the advice of an experienced manufacturer, it is possible to benefit from these and many other advantages offered by stainless steel and to avoid any complications that may arise, since even the best materials can pose problems if misunderstood or misused. For example, when cast iron or galvanised steel meet stainless steel, the contact results in galvanic corrosion in an aqueous environment. Even 316 grade stainless steel, which contains molybdenum and offers an even more resilient option than the more commonly used 304 grade, can be vulnerable to certain chemicals such as hydrochloric acid (HCl) and sulphuric acid (H2SO4). To ensure that all such issues are fully understood, ACO Building Drainage offers accredited CPD, available on a one-to-one basis or to large groups, giving advice on how to 'Specify It Right'. This kind of expert advice can be vital in helping all parties to make the right decisions when specifying drainage systems, particularly in hygiene-critical environments where all opportunities must be taken to protect patient health.
A corrosion resistance check-list, that takes into account factors such as the chemicals that will be present in the drainage system, typical concentration and temperatures, will help ensure that no crucial issue is overlooked during the specification process.
Fabrication processes naturally produce surface defects and imperfections of stainless steel so the correct post fabrication treatment is essential to restore the material to its optimum corrosion resistant state.
The ultimate finishing method is pickle passivation, a controlled corrosion process involving nitric and hydrofluoric acids that removes weld tint and iron embedded impurities introduced in the fabrication process and restores the chromium-rich oxide layer that naturally protects the material.
There are also options to consider regarding finishing, as this ultimately dictates the resistance of stainless steel to corrosion and bacteria; for example, electro-polishing flattens the surface of the stainless steel, which reduces the potential for bacterial growth.
Stainless steel pipework and drainage channels clearly offer the potential to provide healthcare institutions with long, reliable service to maximise budgets and safeguard patients. With the right specification and materials, the defence against bacteria in healthcare environments can be tougher than ever before.
MORE FROM THIS COMPANY
- No related articles listed
OTHER ARTICLES IN THIS SECTION