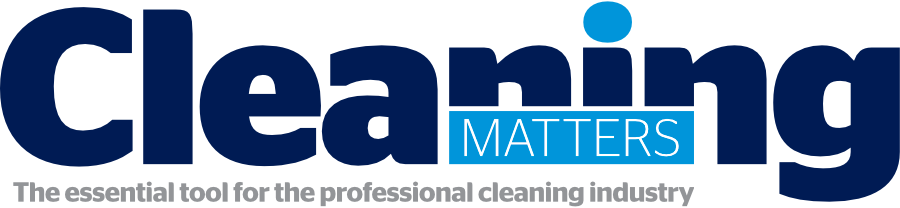
![]() |
Chris Shaw
Editor |
Home> | GENERAL EQUIPMENT & SERVICES | >Accessories | >Spring into the new season |
Home> | FLOORCARE | >General Floorcare | >Spring into the new season |
Spring into the new season
13 February 2023
As the seasons change Scott Saunder discusses the maintenance necessary for facilities managers.

THE TRANSITION from winter to spring is commonly associated with the ‘Spring Clean’ and while many of us may think of decluttering and revamping our homes, it also happens to be the perfect time to reassess your facility.
During winter, the cold weather can result in more damage than would be expected in warmer months, for example freezing water can cause flooring to crack or create potholes. The weather is also unpredictable and doing repairs in the rain can be impractical, plus the limited day light due to shorter days can result in smaller signs of damage going unnoticed.
On the other hand, in spring, the weather is milder and the days are longer. So, it’s the perfect time to assess a facility for damage and resolve any issues that may have occurred during the winter. It can even be the perfect opportunity to go one step further and run an annual risk assessment.
While following a standard risk assessment is always the best place to start when keeping your eye out for damage or signs of wear and tear, a few more insidious problems can creep up following cold or wet weather which are worth paying closer attention to.
Digging deep on the impact of holes
High traffic areas are prone to chips and scratches due to the frequent impact of people crossing the floor and heavy pallet trucks manoeuvring over it everyday. While they may appear minor, if not tackled once they are spotted, they can deteriorate and make a facility appear unsightly.
This deterioration can cause cracks and holes which often result in bigger and more costly problems, particularly on floors that haven’t been treated for a while or on older buildings, which can suffer from structural movement increasing the probability of cracks occurring. In the colder months, these problems can multiply as when water pools and freezes over, the floor surface can be weakened causing cracks and large potholes.
If the damage is spotted and treated quickly, it can be overcome fairly easily. Firstly, the dust and debris would simply need to be cleaned away from the area and then a solids epoxy resin can be used to fill cracks, smooth the surface and prevent the damage from worsening.
Epoxy resins have excellent adhesion to concrete and other surfaces. So once applied, they leave a hard-wearing finish that will protect the floor from moisture when the rainy season returns, and prevent any damage reoccurring.
All over the joint
While scratches, cracks and holes can appear in any area of flooring, it’s worth paying particularly close attention to joints. They are a naturally weaker point in the floor so tend to be more prone to damage from wear and tear. If close attention isn’t paid, they can break and damage the surrounding area too.
However, there are steps facilities managers can take to repair eroded joints. To start with, it’s important to clean and clear the area to prevent any build-up of debris which could cause additional damage later down the line. The extended daylight and mild weather in spring makes it a suitable time to complete this step, especially when it comes to external doorways and joints. Afterwards repair materials, such as a high-quality sealant, can be applied as they are ideal for protecting exposed edges and preventing further deterioration.
Another option is to use a flexible filler, these are suitable for filling in fine cavities. Most traditional flexible filler applications require two steps - reforming joint edges with mortar, and then filling the joint with expansion materials. However, some flexible fillers don’t require joint reforming so the process can be done in one simple step. As an added bonus, fillers can also be sanded, painted or papered over, to create a smooth finish which can help to retain aesthetics.
The ingredients in fillers, such as polyurethane, are also extremely durable meaning that they are strong enough to resist heavy traffic, like forklifts, and keep joints strong throughout the harsher months.
Step outside this spring
In spring, facilities managers are able to spend more time outside assessing the external areas of a facility, but natural lighting can expose more problematic areas.
One of the most common challenges can be sunken flooring. Even if slabs only sink by a few millimetres, they can crack and also become a trip hazard which is not only a risk to workers but can also make it difficult and even dangerous to manoeuvre equipment.
In addition, the protruding edge of staircases can experience wear and tear from heavy traffic. For outside areas, this wear and tear combined with rain, can result in very slippery and dangerous surfaces.
As with any area that starts to show signs of damage, it’s crucial to act before the situation deteriorates. For a sunken floor or damaged steps, epoxy resin mortars - particularly ones with carbon fibre and a ceramic base - can provide a hardwearing and long-lasting solution that prevents accidents and downtime later down the line.
During the spring it is a good idea to take action to get prepared for the cold, wet months, when accidents are more prone to happen. Using anti-slip solutions, such as Glass Reinforced Plastic (GRP) step covers can provide added grip and an extra layer of protection to stop people falling when spills happen or it rains. GRP step covers come with the added benefit that when they are being applied, the area will not be out of action because, unlike paint, there is no drying time.
Keep your operations in line
Warehouses are known for being incredibly busy workspaces, with heavy machinery and a high volume of hazards – and these factors are only amplified during peak periods when traffic soars.
Line marking is one of the best ways to ensure the smooth running of a warehouse as it ensures people know how to move around the facility, indicates hazardous areas - which is particularly vital for visitors and those who are less familiar with a space – and highlights which stock should be stored where. This not only helps to keep individuals safe but also helps increase productivity and efficiency within the space.
However, line marking can become worn and fade overtime, especially during the hectic winter months when footfall and machinery use can increase in preparation for the festive season. On top of this, some paint can fade in the sunlight, so during spring it’s a good idea to touch up line markings and preserve their visibility throughout the summer.
To limit the impact of faded line markings in the future, it is a good idea for facilities managers to source paints and coatings with specialist formulas that provide long lasting colour. Investing in a higher quality product now will ensure that the colours are not only brighter upon application, but that they will remain bright despite the light inevitably hitting them in the sunny season. This will help to limit accidents caused by unclear labelling and will also prevent numerous touch ups and downtime later down the line.
The impact of ignoring repairs
All of these hazards, whether a tiny hairline crack, a wide hole or a sunken floor can result in slips, trips and falls – one of the biggest causes of workplace injury according to Health and Safety Executive.
This means that a lack of maintenance is not only a danger to people, but if left untreated, the damage can become so bad that areas can become inaccessible. This disrupts the flow of traffic around the workspace and consequently impacts productivity within the facility.
Productivity can also be impacted by the downtime involved in the repair job and, naturally, the bigger the damage, the more costly the repair and the longer a space is out of action.
Our own data revealed an average of 27 days are lost a year due to maintenance downtime, with non-fatal injuries costing UK businesses an estimated £18bn a year. So, it’s crucial to carry out a regular risk assessment every spring to stay on top of maintenance and act as soon as possible when a risk is spotted.
Embrace the spring clean season
Annual risk assessments are a vital element of any facilities managers’ job description. So, as seasons change and the days get warmer and brighter, it’s a great opportunity to conduct a survey of a space and implement any repair or maintenance work needed.
Making the most of the weather is the best way to ensure a facility is safe and prevent further damage. This in turn, minimises costly repairs later down the line, maximises productivity and efficiency, and ensures the safety and wellbeing of employees.
Scott Saunders is technical service manager at Watco.
For more information visit www.watco.co.uk.