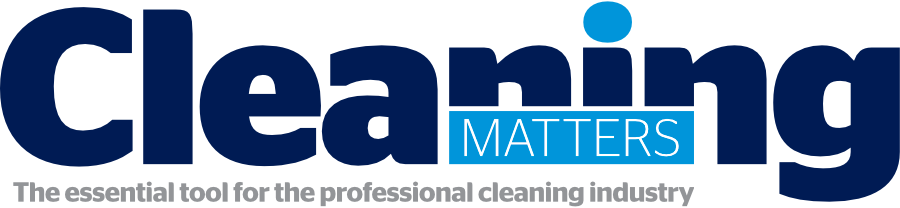
![]() |
Chris Shaw
Editor |
Home> | INDUSTRIAL CLEANING | >Industrial Cleaning machines | >Supporting the manufacturing sector during winter months |
Home> | INDUSTRIAL CLEANING | >Industrial Equipment & Services | >Supporting the manufacturing sector during winter months |
Supporting the manufacturing sector during winter months
08 February 2022
While the 'winter shutdown' provides an opportunity for uninterrupted preventative maintenance and repairs, it is also an important time to conduct deep cleaning and reflect on the manufacturer’s current approach to cleaning routines. Charlotte Burkinshaw believes making the most efficient use of the down period will ensure that your workers return to the safest working environment, all compliance needs are met and production efficiency is sustained throughout the year.
THERE IS clear value in having a properly maintained site and machinery but regular cleaning and thorough deep cleans should be considered equally as important. Manufacturers should take advantage of the downtime as they provide an essential and efficient period to carry out deep cleans of the factory while there is no effect on production - meaning no loss of money during the cleaning process. As there are fewer staff during this time as well, from a health and safety point of view, this is the optimum time to thoroughly clean the floor and machinery. Typically, if conducting a deep clean during normal working days they can present high-risk situations and can disrupt business as usual as machinery would need to be disconnected to clean properly.
In addition to the deep cleans, it’s an ideal opportunity to reevaluate the regular cleaning and maintenance process. If overlooked, then further down the line a degree of equipment inefficiency or failure could be imminent which can leave businesses with unwanted costs and disruptions.
Shutting down to avoid break down
Completing maintenance during production can present many obstacles, stopping staff from using the machinery and often having to delay their work to fit around the engineers.
If major replacements are needed, winter shutdowns allow this to be done outside of production and give time to senior team members to become familiar with new equipment without competing concerns. They also allow for engineers to get the job done quickly and thoroughly.
Giving attention to your equipment will prolong its life-span and prevent any costly, unexpected repairs or replacements later on down the line.
Deep cleans and specialist cleaning
Winter shutdowns for the manufacturing industry provide the perfect opportunity for a reset, allowing for standards to return to their best and to ensure all compliance guidelines and procedures are met. Deep cleans are necessary for the health and safety of staff, maintaining an effective process and ensuring no effect on profits.
Why are deep cleans so important? In regards to machinery, if you have a dirty machine the result may be a dirty product, which will consequently mean an unhappy end customer. If the shop or factory is unclean then there is also a risk of a build up of dangerous or hazardous waste, having an effect on not only the product line, but also the staff on the floors. Deep cleans are at the core of making sure this doesn’t happen. Day-to-day cleaning is only skimming the surface of the dirt and potentially dangerous waste that needs to be removed from factory floors to ensure high-quality work.
If regular maintenance checks and deep cleaning are not conducted, then there is an increased risk of a dirty end product, potential health and safety issues going unnoticed, cross-contamination and infection risk as well as damages to machinery. For example, a specialist team would be cleaning around the machinery thoroughly and may notice a minute crack that might not have been noticed otherwise therefore avoiding having to deal with a costly replacement issue for the business.
Whether working with an in-house dedicated FM manager who is responsible and accountable for overseeing the deep cleaning and regular maintenance, or a contractor to handle the specialist cleaning, there needs to be a full evaluation of the site size - whether just a selection of machines or the entire floor. It’s key to evaluate the safety precautions beforehand depending on how in depth it is. For example, if there are confined spaces or if there is a requirement to go down pits, then there is a higher risk than the shop floor. Equipment will vary according to the space, and may need to be delivered prior to the deep clean. PPE is essential, especially when handling different chemicals, however these will vary depending on manufacturer’s guidelines, so these will need to be scrutinised as there are certain chemicals that should or cannot be used in alternative environments.
The benefits of hiring a contractor ensures that unreachable and often high-risk areas, such as pits, are cleaned by highly trained professionals who have access to specialist treatments. This can give manufacturers the confidence that they are meeting industry regulations and standards and thus avoiding any repercussions or risks to the business or workforce
Reviewing your existing approach to cleaning and maintenance
Downtime can also be used to take a step back and review your current cleaning regime to ensure that it is in line with regulations.
The most important questions you should ask yourself is whether your current regime works and whether you are getting your desired results. If the answer is no to any of those questions, then a winter shutdown is a perfect time to re-think your approach to cleaning and maintenance to ensure that productivity and efficiency is restored when your workers return.
It’s key to understand how your business has changed since you last reviewed your cleaning and maintenance strategy. An expansion, an increase in capacity on site or move to a different site are all significant factors that should transform your approach to maintenance and cleaning. Your strategy needs to be proportionate to the changes that have occurred. If you have increased your capacity on site, then more thorough cleaning needs to take place. If you have invested in new equipment, greater attention needs to be paid to them to ensure workers are familiar with how it works and how to identify when it is failing. If you have expanded and your work-load has increased, you should be clued up on new innovations that could assist your cleaning or maintenance procedures to give more time to production.
When taking these factors into consideration, it will allow for your day-to-day business to operate smoothly and will create a workplace that is easy to navigate whilst employees can feel safe to get the job done.
Embed cleaning and maintenance culture into your factory
It is crucial that upon the return of workers after the winter shutdown that this ethos of increased cleaning and maintenance is embedded across the business. Creating good habits within the workplace will ultimately make life easier for everyone.
Benchmark audits are one way that can help you do this. A benchmark audit every four to six weeks can help identify where cleaning or maintenance practices are failing or can be improved. Staff should know who is responsible for different parts of this procedure and should use a log book to track their actions - this will help pinpoint where an error has occurred.
Manufacturing sites are fast-paced environments where things are constantly changing, communication amongst your workers is central to creating a happy workforce. Being transparent with the actions that need to or haven’t been done facilitates trust between your operatives making it easier to deal with any issues before they arise.
With the recent pandemic, there should be an increased awareness of general cleanliness and hygiene practices. Although previously there was a lack of attention to the general cleaning regime in many workspaces, factory and shop floors, it’s imperative that these are regularly reviewed and a higher standard maintained, which will not only help avoid any cross-contamination, but will also end up saving the business additional machinery costs. Through a deep clean in the winter shutdown and improving the regular maintenance, issues regarding health and safety as well as the condition of machinery can be identified sooner and dealt with. Regularly reviewing the standard cleaning routine can also help discover new innovations, such as new chemicals or equipment that could save the business time as well as money.
Charlotte Burkinshaw, Fidelis Commercial Cleaning, has vast knowledge within administration working in recruitment managing a team of administrators for a number of years and also within the automotive sector looking after Jardine Jaguar Land Rover dealing with the smooth running of the showrooms and HR for the internal employees.
For more information visit www.fidelisgroup.co.uk
- Facilities installation helps save lives
- Rochdale Council wins national competition for local authority cleaning services
- Plans announced for London’s COVID-19 recovery
- The case for rehabilitation
- Dry ice blasting poised for significant growth
- UK-wide plan announced to ensure PPE gets to where it is needed most
- Study demonstrates impact on microbe transmission in hospitals
- Covid infections reduced after mask upgrade
- Restaurant owners fined £10k for hygiene offences
- ICE Cleaning signs deal with China State Construction