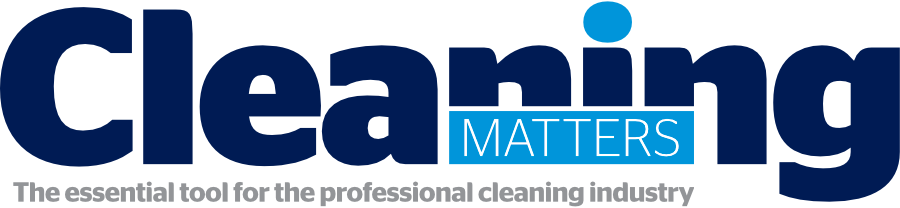
![]() |
Chris Shaw
Editor |
Firing on all cylinders
27 June 2018
Trevor Thomas, project co-ordinator and Mike Howey, site manager, at industrial services specialist Leadec, look at the skill involved in keeping automotive paint shops ultra-clean
When it comes to specialist cleaning, the paint shop environment is one of the most challenging you can find yourself in. Just the smallest particle of dirt within critical areas such as spray booths can cause contamination on the painted bodies which can be the difference between getting vehicles out of the factory and halting production altogether.
Ensuring cleanliness in these environments is a huge challenge and requires a considerably more complex approach than most traditional cleaning methods. Dust is measured in microns, floors must always be completely free of debris, litter and spills, and airborne particulate material must be eliminated.
The standardised process for paint shop operation is to electro-coat the metal car body, apply a surfacer, colour coat and finish with a final clear coat. After each individual coat, there is also a baking process using large curing ovens. This hardens the paint prior to inspection and rectification.
This process rarely changes between different paintshops; therefore the basis of cleaning and the outcome will be similar across most plants. However, the set up of each individual paint shop will vary and this is why a more bespoke approach to technical cleaning is required. At Leadec, we develop a tailored approach to each site, with our methods and techniques dependent on the spray booth design (wet or dry), customer preferences and expectations, oven designs, shift patterns, and production volumes.
A well-oiled machine
Take the typical spray booth as an example. These house multiple robots and conveyors, which all need to demonstrate exceptional levels of cleanliness; indeed, spray booth walls and robots need to be cleaned to a much higher standard than drainage areas within wet spray booths.
Cleaning robots takes additional care and attention. The slightest knock to a machine can position it out of place, potentially disrupting the entire production line. Operatives need to make sure the robot booth is isolated and safe to enter before maintenance is carried out, which means this process must be completed in between shifts. Specialists must therefore be trained in preserving and safeguarding the availability of machinery and always select cleaning equipment based on the properties of the item to be cleaned.
In some environments, Leadec also carries out cleaning of equipment used for cathodic dip coating, an electro-coating process. In most plants a car shell hangs overhead and goes through a series of tanks, dipped in pre-treatment chemicals and phosphate, before being rinsed and painted. All these tanks and robotics require the same levels of cleanliness as spray booths, where more standardised cleaning techniques are not effective enough.
Under pressure
High pressure water jet cleaning is a common technique used in paint shop cleaning. Applications include the underside of paint booths, pre-treatment and eco tanks, and grids. Such areas require frequent deep cleans. Spray booths in particular, have running water beneath them to take away excess paint. Waste can quickly accumulate and build up underneath the grids on the floor, dynatubes and sparge pipes. High pressure water jet spraying is the most convenient and effective method for cleaning these areas. Although precautions must be made and protective clothing worn, this method ensures an effective clean without the use of chemicals.
Sustainability
Disposal is another important factor of paint shop cleaning. Automotive manufacturers are constantly being pushed to save on energy and solvent consumption and become more environmentally friendly in the paint shop. As a result, cleaning processes must follow suit. At one plant, up to 1,000,000 litres of water is recycled every day as part of the effluent removal process.
Sustainability has become such a priority for automotive manufacturers that the market is starting to make this a key aspect of the planning stages of new facility builds. For many businesses, having an environmentally-friendly building is the most cost-effective way of implementing required green standards. There is an opportunity for cleaning and maintenance businesses to work in greater collaboration with customers, advising on optimum building layouts to aid the effective recycling of both air and water through a lean and efficient design.
As paint shops evolve and OEMs coat more sophisticated materials with more advanced, hard-wearing coatings, the impact of contamination increases, and cleaning specialists must ensure they are doing everything possible to eradicate this risk.
- No related articles listed