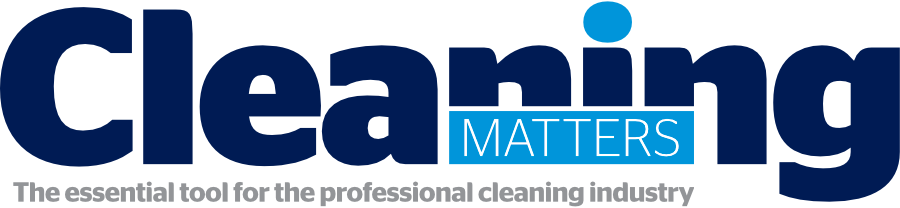
![]() |
Chris Shaw
Editor |
Home> | FACILITIES MANAGEMENT | >Fire & Flood | >Cleaning up after disaster |
Cleaning up after disaster
19 December 2016
The winter months spell increased risk for many businesses, with freezing temperatures and flooding causing potential closure, equipment breakdown and polluting spills. Steps must be taken in the first instance to prevent these incidents where possible and if disaster does strike, quick and effective clean-up plans will minimise any long term damage. Alan Scrafton from Adler & Allan explains
Disastrous weather conditions have unfortunately become a regular fixture of the British winter. For the last few years many homes and businesses have suffered at the hands of flooding which in its wake brings pollution and long-term damage to buildings and their assets. Apart from flooding, freezing temperatures can cause machinery breakdown and burst pipes, also adding to business closure and environmental damage.
While flooding and freezing in themselves can’t be prevented, businesses that know they are at risk should take steps to minimise the effect, with plans in place to clean-up where disaster was unavoidable.
Know your risks
Step 1: Assessment: The first step in preventing the damage winter disasters can cause is understanding what the risks are. For flooding, this takes the shape of a Flood Risk Assessment (FRA), something many businesses should consider, not just those that have already been affected by flooding. An FRA will help identify potential problems up to 60 years in the future, which can then be dealt with before they become an issue with measures such as flood defences, or the creation of a plan to move stock and electronics if you know a flood is coming. In general, risk assessing a business will help tighten up operations and safeguard employees.
Step 2: Planning: As mentioned, by knowing your risks you can plan for disaster. Some incidents, particularly those of an environmental nature, are unavoidable, but their effect can be greatly reduced if proper procedure is in place. When it comes to cleaning, these plans should include having appropriate spill kits on site, essential for businesses that store or transport fuel and other hazardous substances. Planning should also include the processes to minimise downtime, which could include an alternative location to work out of, or allowing office staff to work from home.
Step 3: Preparation: Regardless of disaster, keeping a building and its equipment well-maintained will prevent downtime all-year round and give assets a fighting chance against winter stresses. For example, ensuring pipes and associated tanks are in good working order will minimise the risks caused by freezing. Protective coatings and linings can improve the resilience of tanks and other surfaces, helping them withstand the cold, chemicals and corrosion.
To minimise the water damage and pollution caused by flooding, drain maintenance is essential. In fact, an unblocked drain could make the difference between a building going under water or not.
Step 4: Clean-up: Despite best-laid plans, sometimes disaster is unavoidable. Appropriate and swift clean-up operations will help to minimise site damage and prevent pollution. Where spills are an issue, this process should have started with a spill kit, which for small-scale incidents may be enough to stop pollution and for larger disasters, can act as a first-line of defence before the experts are called in.
Once the flooding or spill has subsided, proper clean-up is essential to bring a site back to pre-disaster standards, minimise downtime, preventing pollution and fines. The first step in this process is assessing the damage, evaluating facilities such as HVAC equipment and taking samples where there is a risk of contamination, particularly if hazardous substances, such as chemicals and carcinogens are on site.
It’s extremely important that human and environmental safety is maintained, with staff kept from exposure to harmful substances and run-off into surrounding water courses avoided. Where sites need full de-contamination there is expert support available, covering everything from ducting to furniture. For high-risk environments, contamination can also be prevented through the use of coatings with anti-bacterial and anti-mould products.
At the time of writing, the winter floods are already taking hold across many parts of the UK. If your business has been affected, or could be in the future, steps to mitigate and deal with disaster effectively will save money long-term, preventing downtime, health and safety and environmental risks.
- Slither into difficult areas
- Having a blast with restoration
- Master plan for disaster clean
- Servicing customers to a high standard
- Don't just clean..sanitise
- SOS guide to flood damage
- Dehumidifying in the face of disaster
- Flood school fears no refurbishment hope for Queensland flood victims
- Preventing the spread of bacteria in flooded areas
- Ready for winter?