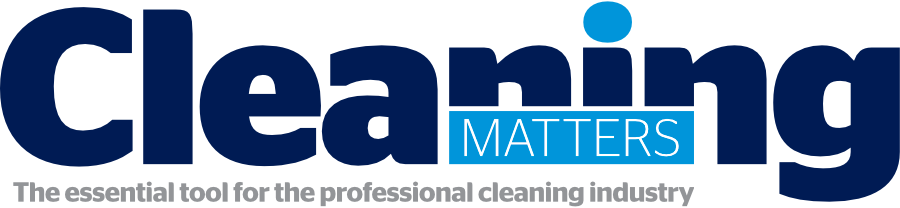
![]() |
Chris Shaw
Editor |
COMPANY PROFILE
Arco Limited
COMPANY DETAILS
Telephone:
01482 222522
Web:
http://www.arco.co.uk
Fax:
01482 218536
Email:
[email protected]
Address:
Arco Limited
P O Box 21
1 Blackfriargate
Hull
North Humberside
HU1 1BH
01482 222522
Web:
http://www.arco.co.uk
Fax:
01482 218536
Email:
[email protected]
Address:
Arco Limited
P O Box 21
1 Blackfriargate
Hull
North Humberside
HU1 1BH