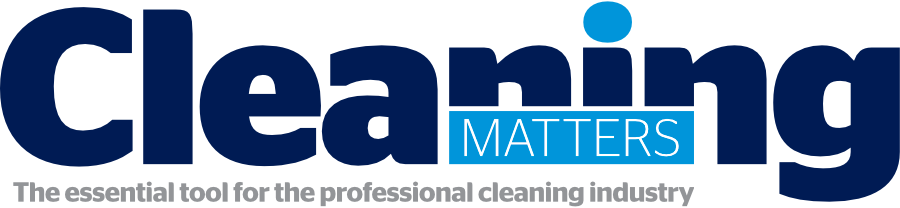
![]() |
Chris Shaw
Editor |
The robotic tank cleaning revolution
11 July 2019
Fintan Duffy, managing director at Re-Gen Robotics, discusses how the introduction of their explosion proof, Ex Zone 0 rated tank cleaning robots are set to raise safety standards in the tank terminal sector
Tank entry is widely recognised as being one of the most hazardous operations in the entire tank cleaning business. Every year as many as 25 people across the UK lose their lives working in confined spaces.
Exposure to hazardous petrochemicals, heat stress, slips and falls are the main risks faced by personnel who manually clean oil tanks. Traditionally personnel have had to enter the hazardous environment of oil tanks to implement inspections, desludge and clean for product change. There are inherent risks to entering a confined space of this nature and although safety regulations and industry standards are high, occasionally accidents occur due to human error and failure of safety devices.
Confined space entry is generally acknowledged as a major safety risk to personnel and it is accepted that it should be kept to a minimum. Current health & safety legislation stipulates that ‘a person shall not carry out work in confined spaces if it is reasonably practical that it can be avoided’. And companies cannot afford to be negligent where human life is concerned. As well as the obvious tragedy and devastation to a family when a life is lost, there is a negative impact to companies associated with loss of life through confined space working; there is damage to organisational reputation, company and shareholder value and the risk of corporate manslaughter charges to consider.
Striving for safer methods
The industry is striving for new, safer methods of cleaning, inspection and assessment and there is a very real appetite across the board, for “no man entry” tank cleaning. We are being told that some of the top oil companies in the UK have been instructed by their boards to find an alternative to ‘man entry’ cleaning, with some postponing tank cleans on petrol tanks, until they have found a solution that guarantees the health and safety of personnel.
Most companies have used some form of robotic tank cleaning but invariably at points during the cleaning process, personnel have had to enter the tank to fix ramps and manually complete the wash out of the tank with a lance, as the best tank cleaning robot to date, has no auger or jetting.
Fully, remote controlled robotics is where we believe we can make a monumental difference to the petrochemical industry. Earlier this year Re-Gen Robotics, a sister company of Re-Gen Waste, one of Europe’s most advanced materials recovery facilities, launched the first Zone 0 EX Certified, remote controlled, ‘No Man Entry’ robotic tank cleaning company in the UK.
The new state-of-the-art, automatic tank cleaning system – which is comprised of explosion proof and intrinsically safe tank cleaning robots – aims to eradicate fatalities in the UK petrochemical industry, eliminating human exposure to confined spaces and hugely decreasing all risk categories.
Fully, remote controlled robotics
We have invested £1.5M in two purpose-built, fully compliant, Ex Zone 0 rated machines; one designed to de-sludge, wash and clean large-scale tanks and a second, lightweight and highly portable compact unit suitable for use on smaller sites and underground storage tanks and containers, including petrol forecourts, interceptors and process tanks.
Re-Gen Robotic’s closed loop cleaning system is fully compliant with existing safety legislation and is said to reduce cleaning time by up to 45 per cent, significantly decreasing downtime and loss of production whilst the facilities are not operational.
The Ex-zone rated equipment is effective, reliable and provides predictable cleaning times, meaning the tank is brought back into operation quicker and reduces the need for additional tank capacity, permitry delays and additional support teams.
Safety and protection of personnel during tank cleaning services are of the utmost importance. At no time during the Re-Gen Robotics cleaning process will there be a need for human presence in the confined storage container. Our technical operator remains a safe distance away in the Zone 2 control unit, where they can monitor activity and progress through a series of ATEX cameras fixed to the equipment placed inside the tank being cleaned.
Suitable for cleaning oil and chemical tanks, the robot is designed to enter through a standard 600mm manhole via an extending ramp. The fully automated, highly mobile, remotely controlled, self-sufficient combination of tanker, 4,800 C/M3 per hr vacuum and specially designed 3,500 PSI jetting water nozzles play a vital part in the cleaning process. This robotic system has the power to clean even the biggest oil tanks with minimum hassle, delivering maximum results.
There is no human exposure to sludge or waste materials during the cleaning process and once cleaning is complete, the robot safely exits the container via its ramp and is returned to the control unit.
At Re-Gen Robotics we believe the economic, environmental and safety benefits to the Tank Terminal Sector are extensive and that the market is ready for it.
- No related articles listed