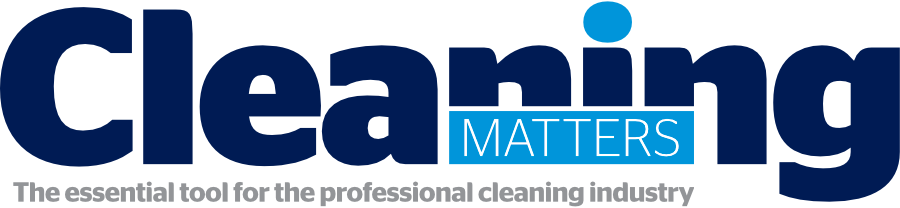
![]() |
Chris Shaw
Editor |
Fall protection: Understanding BS 8681 | 01/09/2025 |
---|---|
The British Safety Industry Federation (BSIF) Height Safety Special Interest Group (BSIF HSG) has unveiled an overview of the new Personal Fall Protection Equipment Standard, BS 8681, which outlines its implications for the industry and those it impacts. FALL PROTECTION equipment plays a crucial role in safeguarding workers from the risks associated with working at height, which remains one of the leading causes of workplace fatalities and injuries in the UK. The use of proper fall protection systems, combined with rigorous training and adherence to safety standards, is essential in mitigating these dangers. The introduction of the new British Standard, BS 8681 marks a significant step forward in this area. Officially titled "BS 8681 - Personal fall protection equipment – Anchor systems – Specification for provider competence", this Standard sets out clear guidelines for the industry, emphasising competence and safety across all aspects of fall protection systems. By focusing on the necessary skills, knowledge, and experience required at every stage of fall protection—from design to installation, inspection, and training – BS 8681 aims to enhance safety and reduce the high number of accidents and fatalities associated with working at height. A complement to BS 7883 BS 8681 has been designed to work in tandem with the existing BS 7883 standard, which focuses on the technical aspects of designing, installing, and inspecting personal fall protection anchor systems. While BS 7883 addresses the hardware and structural integrity of these systems, BS 8681 broadens the focus to include the competence of all professionals involved. This new Standard emphasises that every person in the "safety chain"—from system designers to installers, inspectors, and trainers—must have the necessary skills, knowledge, and experience to ensure that fall protection systems are safe and effective. Competence and responsibility One of the key objectives of BS 8681 is to raise the competence levels across the industry. The Standard aims to ensure that those involved in the design, installation, and inspection of fall protection systems are thoroughly qualified. For instance, System Designers, whose role was first introduced in BS 7883, must ensure that the systems they design are not only compliant with safety standards but also fit for purpose throughout their operational life. This includes considering factors such as safe construction, use, rescue, and inspection. BSIF HSG member Elizabeth Rickard of Spring Structural Ltd comments: "BS 8681 is a promising step forward in addressing industry challenges, particularly in the realm of personal fall protection systems. Generally, it takes two years to train a System Designer to simply provide the pertinent information. "Given my experience in training system designers over that two-year period, BS 8681 could significantly streamline onboarding by offering a clearer framework for competence. It also has the potential to improve collaboration with other stakeholders by establishing shared expectations. Furthermore, by ensuring that upstream information is more reliable and standardised, it can help reduce both rework and risk throughout the design and implementation process." BSIF HSG member Harvey Dun of Time Consulting adds: "BS 8681 is a good start to assist in setting the benchmark of competency for people involved in the fall protection industry. Dun explains: "The Standard provides the purchasers of products and services, often referred to as the duty holder, with guidance check lists to confirm the provider they engage is suitably competent. These checklists may be adopted by Safety Schemes in procurement (SSIP) when assessing those providers operating in the fall protection industry." Manufacturing and testing Manufacturers also play a crucial role under BS 8681. The Standard provides clear guidelines on the necessary steps to ensure that anchor devices and other components meet stringent safety requirements. This involves rigorous testing, certification, and documentation to guarantee that these products can withstand the demands of real-world use in high-risk environments. Training and qualifications Training and competency are central themes in BS 8681. The Standard supports the development of qualifications, such as the Level 3 apprenticeship and NVQ Level 3 for permanent fall arrest technicians, which is part of a broader effort to professionalise the industry. This initiative, driven by BSIF HSG, aims to close the skills gap and ensure that all workers in the fall protection industry are equipped with the necessary knowledge and experience to perform their roles effectively. BSIF HSG member, John Hynes of Autumnal Services Ltd, comments: "Formal, sector-specific qualifications, such as the NVQ Level-3 for installers, should raise the quality of installers and inspectors. And the introduction of BS8681 will make it clear to Duty Holders and others that there are minimum acceptable competency levels." Inspection and auditing BS 8681 emphasises the importance of thorough inspection and auditing processes to maintain the integrity of fall protection systems. Inspectors must be highly skilled and knowledgeable, capable of identifying potential hazards that could compromise safety. Regular audits, both internal and external, are recommended to ensure ongoing compliance with the Standard, thereby ensuring that systems remain safe throughout their operational life. A positive impact on the industry The introduction of BS 8681 is expected to have a profoundly positive impact on the fall protection industry. By setting higher standards for competence and safety, it aims to drive a cultural shift towards greater accountability and professionalism. Duty holders can now have greater confidence that they are working with competent professionals who can deliver safe, compliant, and effective fall protection systems. BSIF HSG member Ben Haughton of Ocean Technical Safety Services Ltd comments: "The fall protection industry is entering a new era; with the publication of BS 8681and the support of BSIF, professional competency standards within the industry are going to be raised and in turn, greatly improve worker safety." Hynes adds: "There will be a period where these new expectations and requirements are a challenge to our sector, but in the long term, they are completely reasonable and readily achievable, and they should lead to a significant improvement in the quality of design, installation and record keeping we see for fall protection systems." Dun concludes: "My message to the companies and people who procure installation, inspection and consultancy services is to use BS8681 as part of the tools available in their due diligence process of selecting competent contractors." To view the BSIF's overview of BS 7883, designed to help the understanding of best practice for those designing, installing, maintaining and inspecting anchor devices and systems, visit: www.bsif-heightsafetygroup.org The BSIF (HSG) has produced a webinar that brings together industry experts to discuss the requirements of providers within the industry. The webinar is available via the following link:- BS 8681:2024 Personal fall protection equipment – BSIF HSG Webinar – BSIF Height Safety Group. For more information: https://www.bsif-heightsafetygroup.org/ |
|
|
|
Buying PPE? Look for a Registered Safety Supplier | 27/06/2018 |
Frank Angear, general manager for the British Safety Industry Federation (BSIF), discusses the benefits of its Registered Safety Supplier scheme The British Safety Industry Federation (BSIF) is the trade association for all organisations involved in the supply of Personal Protective Equipment (PPE) and safety related products and services. From this position, the Federation believes strongly that occupational users have a right to expect their safety equipment to be of good quality, to protect them adequately, and to be fully compliant with all relevant regulations and requirements. Furthermore, the BSIF believes passionately that all users, specifiers and purchasers of such equipment deserve to be serviced and supported by capable, knowledgeable and responsible suppliers. All member businesses of the BSIF involved in the supply of PPE and related safety equipment are required to sign up and adhere to the requirements of the Registered Safety Supplier Scheme which places a number of obligations on the organisation. They are required to:
This provides a significant layer of confidence for users and a differentiator for suppliers from competitors who do not make such commitments. When sourcing PPE and related occupational safety equipment buyers can look for the Registered Safety Supplier Scheme logo, (shown here). End user companies can register as supporters of the scheme on the dedicated supporter’s website: www.registeredsafetysupplierscheme.co.uk |
|
|
|
Fracking clean-up concerns | 17/10/2017 |
The British Safety Industry Federation (BSIF) general manager Frank Angear looks at the challenges of controlling site spills when it comes to shale gas extraction At the moment UK energy supplies are provided by natural gas (40%), coal (10%), nuclear power (25%), biomass (12%) and renewables (12%). With climate change targets, the closure of coal mines, concerns surrounding nuclear power and the high cost of renewables, Britain needs additional diverse sources of energy. Enormous effort is going into new technology such as clean gas power stations, thermo-voltaic light, new battery developments and seismic surveying, which will alter the relative attractions of nuclear, gas, and renewable sources, but predicting which technology will meet the increased demand at a sensible cost with acceptable carbon emissions is difficult. One option under consideration is the extraction of shale gas through a process known as "fracking". It is argued that the cost of British shale gas would be low because it is believed that there are large volumes, it is relatively easy to extract and the cost of distribution is low as the gas infrastructure is already in place. But a new industry would bring its own set of requirements on pollution control to avoid environmental spills. All energy sources, gas, coal, nuclear, biomass, and renewables carry environmental risks. Environmental concerns around shale gas focus on:
However, a major concern is the heavy goods vehicle transportation of the large volumes of flowback water created. The BSIF Liquid Pollution Control Group - which makes recommendations for tackling spills control when extracting shale gas - agrees with leading shale gas companies that the water should be processed on site. Contamination of groundwater is of course a risk, but a peer reviewed study of contamination of groundwater by Duke University (The Effects of Shale Gas Exploration and Hydraulic Fracturing on the Quality of Water Resources in the United States by Avner Vengosh et al) found fracking has not contaminated ground water. However the study did find that accidental spills of fracking waste water could be dangerous to surface water in the area. If extraction of shale gas is given the go-ahead in Britain, the BSIF Liquid Pollution Control Group makes the following recommendations:
|
|
|
|
“Anyone can sell Safety but you wouldn’t buy Safety from anyone”. | 22/05/2017 |
The British Safety Industry Federation (BSIF) is dedicated to eliminating non-compliant, unsafe, counterfeit and illegal safety products from the UK market. BSIF CEO Alan Murray explains how its Registered Safety Supplier Scheme provides a quality assurance scheme for the purchase of genuine personal protective equipment (PPE) that will help to keep people safe and healthy at work If the outcome of an employer’s risk assessment includes the necessity for Personal Protective Equipment (PPE) it is the law that it must provide adequate protection against the hazard and it must be suitable for the individual. The Registered Safety Supplier Scheme, administered by the BSIF, historically focused on the threat posed by fake and counterfeit products and fake and counterfeit certification. However, in addition to this problem, a much more pernicious threat has become apparent over the last 18 months and that is the failure of PPE to match the performance that the CE certification claims and crucially the performance that users anticipate. We have seen increasing evidence that PPE products in the market fail to perform. Many products in Category I such as leather gloves contain Chromium VI and Azo dyes and therefore fail the CE Basic Requirements of Safety and Health where the PPE itself actually contains a threat to the user. This has been the subject of a National Trading Standards investigation this year. Perhaps the most startling examples come in Category II (which include safety footwear, safety helmets and high visibility clothing) where the performance claims from the original, one time, type testing are just not being achieved. It has therefore become absolutely necessary to strengthen the terms of the Registered Safety Supplier Scheme to address this. The number of non-compliant, illegal and poorly performing safety products offered for sale in the UK market is significant and all organisations and individuals sourcing PPE and related equipment need assurance that the markings, documentation and claims for the performance of the product are still valid. The BSIF Registered Safety Supplier Scheme is being strengthened to provide assurance to PPE customers and users that only compliant and correctly performing products are supplied. A Registered Safety Supplier Scheme member…
Who benefits …
Is your supplier a Registered Safety Supplier Scheme member? Look for the logo. A full listing of Registered Safety Suppliers can be found on www.bsif.co.uk/registered-safety-supplier Anyone can sell Safety but you wouldn’t buy Safety from anyone. Insist on a Registered Safety Supplier for your Personal Protective Equipment.
|
|
|