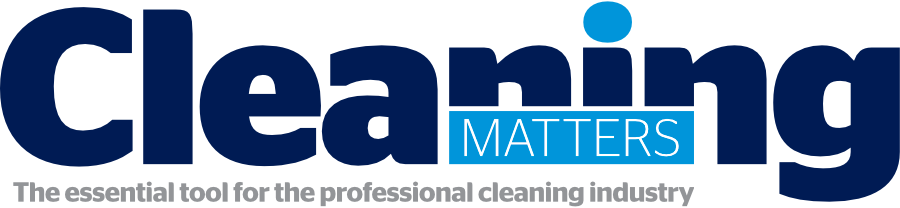
![]() |
Chris Shaw
Editor |
1/9 (1 to 10 of 81)
HSE announces legionella bacteria guidance update | 16/04/2024 |
---|---|
THE HEALTH & Safety Executive (HSE) has updated its technical guidance publication 'The control of legionella bacteria in evaporative cooling systems' (HSG274: Part 1). According to the HSE, the guidance for managing the legionella risk presented by these systems has been improved in several areas.
|
|
|
|
Recycling company fined for poor health and safety management | 19/10/2021 |
A WASTE and recycling company has been fined after HSE inspectors discovered widespread poor management of health and safety risks at their site in West Drayton, London. Westminster Magistrates Court heard that, on 21 March 2019, inspectors attended Iver Recycling (UK), Holloway Lane, West Drayton, to carry out a routine inspection, where they discovered widespread risk to employees and poor health and safety management of the site. HSE revisited the site on 1 April 2019 with electrical engineering, mechanical engineering and civil engineering specialists to assess the site. In total, HSE issued nine Prohibition Notices and seven Improvement Notices. Conditions were so bad that an investigation was conducted to help understand the underlying causes of the conditions seen. The investigation concluded that a lack of competent advice, risk assessment and poor management had led to deterioration of conditions on site, despite previous enforcement being issued by HSE. Iver Recycling (UK) failed to appear at the hearing on 16 September 2021, and the case was heard in their absence. The court found that HSE’s case, a breach of Health and Safety at Work etc. Act 1974 Section 2(1) had been proved. The company was issued with a £200,000 fine and order to pay cost of £7,125.72 and the victim surcharge of £170. Following the hearing, HSE inspector Sarah Pearce said: “Companies should be aware that if they fail to operate their businesses in a manner which protects the health and safety of those who work there, HSE will pursue those responsible to the highest possible level. The conditions seen at this site should not occur in 21st-century Britain.” |
|
|
|
Farm fined after employee permanently blinded by disinfectant chemicals | 25/11/2019 |
Beechdean Farm Limited has been fined following an incident in which an employee was permanently blinded by corrosive chemicals used in cleaning. High Wycombe Magistrates’ Court heard that in August 2017, an employee was cleaning the walls of the dairy farm at Old House Farm in North Dean, Buckinghamshire, using a corrosive disinfectant DM CiD, which contains potassium hydroxide. The pump sprayer being used unexpectedly developed a fault and ruptured into the face of the employee. His face became covered in the caustic and corrosive disinfectant, rendering him permanently blind in both eyes. An investigation by the Health and Safety Executive (HSE) found that Beechdean Farm Limited failed to plan and supervise the use of chemicals for cleaning the dairy and did not have effective emergency arrangements in place. Beechdean Farm Limited of North Dean, Buckinghamshire pleaded guilty to breaching Section 2(1) of the Health and Safety at Work Act 1974 and has been fined £8,000 and ordered to pay costs of £11,879.94. Speaking after the hearing, HSE inspector Stephen Faulkner said: “While it was possible for both the pump sprayer and the chemical to be used for cleaning, this incident could so easily have been avoided by implementing correct control measures, safe working practices and appropriate emergency arrangements. “Agriculture is an industry with a high accident rate, and the chemicals and activity involved in this incident are common in dairy farming, so this case should send a message to farms about the dangers of working with chemicals. “Companies should be aware that HSE will not hesitate to take appropriate enforcement action against those that fall below the required standards.” |
|
|
|
Great Britain's annual injury and ill-health statistics announced | 05/11/2019 |
The number of injuries and incidents of ill-health in workplaces across Great Britain is still too high, new statistics show. The annual report by the Health and Safety Executive (HSE) includes statistics for work-related ill health, workplace injuries, working days lost, enforcement action taken, and the associated costs to Great Britain. Figures show that around 581,000 workers sustained non-fatal injuries in 2018/2019, with 1.4 million workers suffering from work-related ill-health. The statistics, compiled from the Labour Force Survey (LFS) and other sources, illustrate that in Great Britain in the 2018/2019 period there were;
The estimated economic cost to Great Britain totalled £15 billion in 2017/2018. Despite Great Britain continuing to be one of the safest places to work, the reported figures highlight there are still areas to be improved upon to prevent fatalities, injuries and ill-health. The figures highlight the scale of the challenge HSE currently faces in making Britain a healthier and safer place to work. In response to the report, Martin Temple, HSE Chair, said: “Great Britain’s position as one of the safest places to work should be a point of pride for us all, but these figures show there is still much to be done to ensure workers go home both healthy and safe. “These figures should highlight to us all the vital importance of managing risk and promoting behaviours to improve the standard of good health and safety practice in the workplace. “We must all share the responsibility of ensuring everybody is aware of what they need to do to work right by preventing work-related incidents, and making our places of work healthier and safer for everyone.” The full annual injury and ill-health statistics report can be found on HSE’s website. |
|
|
|
Recycling company fined after employee suffers amputation | 22/10/2019 |
A waste recycling company has been fined after an employee lost part of his arm in a conveyor belt. Lincoln Crown Court heard on 26 April 2015 that the employee of Mid-UK Recycling Ltd was working as a line operator in the building known as Unit 4 MRF (Material Recovery Facility). On the morning of the incident, blockages had occurred on this line and waste had become wrapped around the axle stopping a lower conveyor. It was whilst removing waste from this axle that the employee’s glove got dragged into the in-running nip between the belt and the powered roller of the conveyor. This resulted in his left arm being amputated above the elbow. An investigation by the Health and Safety Executive revealed that the company had failed to prevent access to dangerous parts of the conveyor. The castell key system had essentially been bypassed allowing the system to be operated in automatic mode with persons still inside the enclosure. Mid UK Recycling Limited (now known as MUKR Limited) of Summit House, Quarrington, Sleaford, Lincolnshire, NG34 8RS pleaded guilty to a breach of section 2 (1) of the Health and Safety at Work etc. Act (1974) and was fined £1.275 million and ordered to pay costs of £45,065.59 Speaking after the hearing, HM inspector Scott Wynne said: “This incident could so easily have been avoided had the company ensured that the system designed to keep people away from dangerous machinery was properly maintained. Companies should be aware that HSE will not hesitate to take appropriate enforcement action against those that fall below the required standards.” |
|
|
|
Director of waste company convicted | 04/10/2019 |
The director of a waste management company has been ordered to carry out unpaid work after an employee was critically injured. Poole Magistrates’ Court heard that on 18 April 2017 Justin Tinsley, then aged 33, had only been employed by Mike Toon Ltd for a few weeks when he was trapped between a telehandler and a gate post at the company yard on Dawkins Road in Poole. Mike Toon Ltd processed and recycled builders’ waste and soil at the yard. Justin was struggling with a manoeuvre and the machine became stuck. With the engine running and the door blocked Justin climbed out through the window to allow Mr Toon to free the machine. However, the machine moved unexpectedly, and Justin was crushed between the machine and a gate post. Justin was unconscious in hospital for some weeks and has never fully recovered from his crush injuries. An investigation by the Health and Safety Executive (HSE) found Justin was being trained to drive a telehandler by the company owner and director Michael Toon. The investigation found several serious long-term faults with the telehandler including some relating to braking. Michael Toon of Poole Road, Bournemouth pleaded guilty breaching section 37 of the Health and Safety at Work etc Act 1974; that being a director of Michael Toon Ltd he failed to discharge his duty under section 2(1), the offence being committed with his consent or connivance or being attributable to his neglect. He was given a 120 hours unpaid work community order and ordered to contribute to costs of £1500. HSE inspector Ian Smart said: “Michael Toon was well aware of the unsafe condition of the telehandler yet allowed it to be used by an inexperienced employee. “HSE promotes safe-stop procedures where drivers should apply the parking brake and turn off the ignition before exiting any mobile machinery. Justin could not do this as the telehandler was in such poor mechanical condition. The law requires mobile machinery to be in safe working order at all times. Maintenance is not optional. This accident could easily have been prevented.” |
|
|
|
Spill control company sentenced after worker suffers life-changing injury | 09/08/2019 |
A company that manufactures absorbents and spill control products has been fined after an agency worker suffered a life-changing injury to her hand when it was caught in a rotating fan blade. Manchester Magistrates’ Court heard how, on 18t October 2017, the 34-year-old agency worker had been working her second shift at the NPS Worldwide UK Limited site at Oldham. While removing a blockage inside the filling machine she had been operating, her fingers became caught in an unguarded rotating fan. The agency worker lost parts of all of her fingers on her right hand, sustained extensive scarring to her stomach following an unsuccessful attempt to generate new skin growth to save her fingers, and continues to suffer post-traumatic stress disorder as a result of the incident and the injuries sustained. An investigation by the Health and Safety Executive (HSE) found the fan had not been suitably guarded, putting employees and agency workers at risk. The company had failed to carry out a suitable risk assessment and provide adequate information, instruction and training to workers. No first aid provision was available on the night shift when the incident occurred, and this contributed to the injured person suffering further as incorrect first aid was administered. NPS Worldwide UK Limited of Vulcan Business Park, Derker Street, Oldham, pleaded guilty to breaching Section 2(1) and 3(1) of the Health and Safety at Work etc. Act 1974 and Regulation 3(2) of the Health and Safety (First Aid) Regulations 1981. The company was fined £28,000 and ordered to pay costs of £7,771. HSE inspector Sharon Butler said after the hearing: “This injury could have easily been prevented and the risk should have been identified. “Employers must make sure they properly assess and apply effective control measures to minimise the risk from dangerous parts of machinery.” |
|
|
|
Recycling firm fined after worker loses fingers clearing baler blockage | 09/08/2019 |
A Manchester based company has been fined after an employee seriously injured his hand and lost two fingers whilst operating a baler at their site in Bradford Street, Bolton. Manchester and Salford Magistrates’ Court heard how, on 2 October 2018, the worker, who had been employed at Wrapp Recycling Ltd for just eight weeks, attempted to clear a blockage in the hopper of the machine while it was switched on. After removing the guard he leaned into the machine and moved the blocked plastic. The ram then activated, crushing his hand. The incident caused extensive damage to his hand, including the amputation of two fingers for which he is still undergoing treatment. He has since been unable to return to work. An investigation by the Health and Safety Executive (HSE) found the company had installed a removable guard as blockages in the machine occurred frequently. The employees were not informed of the dangers of accessing the hopper while the power was on and HSE found was common practice to clear the machine by hand with the machine still running. The investigation also found there was no suitable risk assessment in place which would have identified the necessary control measures needed, such as a fixed guard and a safe lock off. Wrapp Recycling Ltd of Bradford Street, Bolton pleaded guilty to breaching Section 2 (1) of the Health and Safety at Work etc. Act 1974 and was fined £13,000 and ordered to pay costs of £5,951.90. Speaking after the hearing, HSE Inspector Catherine Lyon said: “This incident could so easily have been avoided by simply carrying out correct control measures and implementing a safe system of work. “Companies should be aware that HSE will not hesitate to take appropriate enforcement action against those that fall below the required standards.” |
|
|
|
Fine for inadequate welfare facilities on site | 09/08/2019 |
A Stockport construction company has been prosecuted after failing to ensure suitable welfare facilities were provided for workers on site. Manchester Magistrates’ Court heard that R & S Builders (Mcr) Ltd had been issued with multiple Improvement Notices, following an inspection by a Health and Safety Executive (HSE) inspector at the company’s site at Great Underbank, Stockport on 7 July 2018. The company subsequently complied with the Improvement Notices that had been served for fire safety and respiratory risks, but failed to comply with the minimum standards of health, safety and welfare on site. An investigation by the HSE found that welfare facilities on site had been in a poor condition, in particular there being no hot or warm running water, and that the company did not provide evidence of compliance with the Improvement Notice within the deadline. R & S Builders (Mcr) Ltd was previously subject to enforcement action by HSE in 2017 that included an Improvement Notice in relation to the absence of adequate welfare provisions at a different site. R & S Builders (Mcr) Ltd of Sovereign House, Stockport Road, Cheadle, pleaded guilty to breaching Section 21 of the Health and safety at Work etc. Act 1974 and Regulation 13(4) of the Construction (Design and Management) Regulations 2015. The company was fined £8,000 and ordered to pay costs of £1,814.90. HSE inspector Chris Brookes-Mann said after the hearing: “Companies should be aware that HSE will not hesitate to take appropriate enforcement action against those that fall below the required standards. Furthermore, companies that fail to comply with an Improvement Notice in the time allowed can expect to be prosecuted since this is a criminal offence in its own right regardless of the circumstances under which the original Improvement Notice was served.” |
|
|
|
HSE releases annual workplace fatality figures | 16/07/2019 |
The Health and Safety Executive (HSE) has released its annual figures for work-related fatal injuries for 2018/19 as well as the number of people known to have died from the asbestos-related cancer, mesothelioma, in 2017. The provisional annual data for work-related fatal injuries revealed that 147 workers were fatally injured between April 2018 and March 2019 (a rate of 0.45 per 100,000 workers). There has been a long-term reduction in the number of fatalities since 1981. Although 2018/19 saw an increase of 6 workplace fatalities from 2017/18, the number has remained broadly level in recent years. Following the release, HSE chair Martin Temple said: “Today’s release of workplace fatality statistics is a reminder that despite the UK’s world leading position in health and safety, we cannot become complacent as we seek to fulfil our mission in preventing injury, ill health and death at work.” The new figures show how fatal injuries are spread across the different industrial sectors:
The figures also indicate those sectors where the risk of fatal injury is greatest:
Martin Temple added: “These statistics also remind us that, in certain sectors of the economy, workplace death remain worryingly high. Agriculture, forestry and fishing accounts for a small fraction of the workforce of Great Britain, yet accounted for over 20 per cent of worker fatalities in the last year. This is unacceptable and more must be done to prevent such fatalities taking place. “Whatever the sector, we should remember that any change in numbers provides little comfort to the family, friends and colleagues of the 147 whose lives were cut short this year while doing their job.” The three most common causes of fatal injuries continue to be; workers falling from height (40), being struck by a moving vehicle (30) and being struck by a moving object (16), accounting for nearly 60 per cent of fatal injuries in 2018/19. The new figures continued to highlight the risks to older workers; 25 per cent of fatal injuries in 2018/19 were to workers aged 60 or over, even though such workers made up only around 10 per cent of the workforce. In addition, there were also 92 members of the public fatally injured in incidents connected to work in 2018/2019, approximately a third of which took place on railways. Mesothelioma, which is contracted through past exposure to asbestos and is one of the few work-related diseases where deaths can be counted directly, killed 2,523 in Great Britain in 2017- a broadly similar number to the previous five years. The current figures are largely a consequence of occupational asbestos exposures that occurred before 1980. Annual deaths are expected to remain broadly at current levels for the rest of the decade before beginning to reduce in number. |
|
|